The objective of this technical paper is to offer an introduction to integrating each motion and sensing component into a low-profile robot joint. The paper will cover design options for the motor, encoder, brake, gear assembly and servo drive.
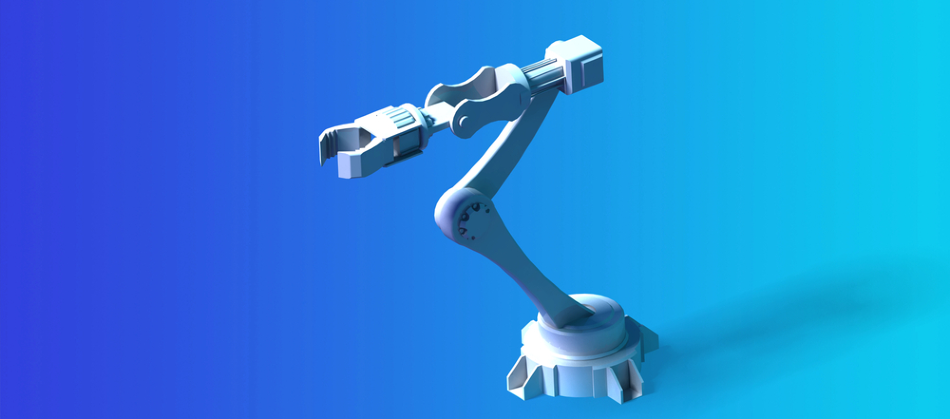
Image Credit: Shutterstock/Shishir Gautam
Background
As robotic and robotic-assisted commodities spread through the industrial, commercial, and medical markets, novel design approaches are beginning to emerge, which focus on smaller and more compact assemblies embodying high accuracy and reliability.
To accomplish this, one design solution is the development of an integrated robot joint containing a direct drive frameless motor kit, precision zero-backlash strain wave gear set, high-resolution encoder kit and an ultra-miniature servo drive, all in one housing. This approach towards component integration enables a low weight and extremely low axial height, allowing a particularly low profile in comparison to prepackaged motors, gearboxes and encoders assembled.
Integrated Robot Joint
Figure 1 below presents an integrated robot joint. The design has taken advantage of low axial height components, rendering the assembly particularly compact. The assembly also comprises an encoder that provides high resolution and precision on the output, in addition to a medium-resolution encoder on the rear of the motor.
.jpg)
Figure 1. Integrated Robot Joint
Figure 2 below indicates the principal components in this integrated robot joint. It comprises the following properties:
- Precision low-profile strain wave gearing with zero backlash
- Frameless brushless motor kit
- Medium-resolution incremental optical encoder kit on the motor side
- High-resolution incremental optical encoder kit with MMA near-absolute technology on the output side
- Front, center, and rear housing components
- A flanged output shaft to interface with nearby assemblies
- Precision bearings for the input shaft, gearing, and output shaft
- Axial through hole for simplified robot joint wiring
.jpg)
Figure 2. Cross Sectional View of Integrated Joint
Figure 3 below depicts another technique, which utilizes two absolute inductive encoders. Bearing similarities to the construction of the joint in Figure 2, there is an encoder on the motor side (input) and the output side after the gear. This assembly also comprises an electromechanical brake for holding when the power has been shut down.
.jpg)
Figure 3. Integrated Robot Joint with Brake
Figure 4 below describes the principal components in this integrated robot joint. It includes the following features:
- Precision low-profile strain wave gearing with zero backlash
- Frameless, slotless, zero cogging brushless motor kit (refer to the definition below)
- Medium-resolution absolute inductive encoder kit on the motor side
- High-resolution absolute inductive encoder kit on the output side
- Front, center, and rear housing components
- A flanged output shaft to interface with nearby assemblies
- Precision bearings for the input shaft, gearing, and output shaft
- Electromagnetic brake
- Axial through hole for simplified robot joint wiring
.jpg)
Figure 4. Integrated Robot Joint
Precision Gearing
Robot joints embody different reflective loads and inertia in accordance with position. Utilizing a gear reduction augments output torque, mitigates the servo tuning consequences of a large change in inertia with position, and permits the utilization of smaller motors that require lower power and promote efficiency.
Backlash is an issue that is caused using conventional gear reducers. While a higher gear ratio overcomes certain torque and inertia obstacles, the consequent backlash causes positioning faults and potential tuning problems. There are two readily available gearing types that embody zero-backlash: strain wave gears and cycloidal drives. These two approaches implement a unique mechanical design, which constantly maintains contact between sub-components. Contemporary enhancements in design and packaging have generated particularly low-profile gearing sets in comparison to earlier offerings from the supply base.
Figure 5 below depicts a low-profile strain wave gear set. Cycloidal gear suppliers provide similar products.
.jpg)
Figure 5. Strain Wave Gear Set
Frameless Brushless Motor Kit
The assemblies in Figures 1 to 4 (above) utilize frameless brushless motor kits, also referred to as torque motor kits. These kits comprise an electromagnetic stator and a permanent magnet rotor functioning as a conventional, synchronous motor via a three-phase servo motor drive.
A rapidly growing design trend is the utilization of a motor kit inside the integrated robot joint as a means of driving a high-ratio gear set. Direct drive motor kits possess higher pole counts that augment torque output and large through holes for optimizing mechanical packaging. These kits are configured like a ring, satisfying high torque requirements and simultaneously conforming to low-profile constraints.
Robot joint output is typically slow. Indeed, 20 rpm would represent a rapid robot joint move. After a typical gear ratio of 150:1, the input speed (motor rotating speed) is 3000 rpm. This is not particularly high for an electric motor, but only if the appropriate impedance is chosen to match the available voltage.
Figure 6 below describes an Agility™ slotless, low profile, large through hole, frameless motor kit.
Slotless motors abolish cogging torque and render the fine motion of the robot smooth and predictable. They also embody low magnetic core losses, enabling the attainment of high rotational speeds, and possess large through holes, which makes them particularly appropriate for robot joint applications.
Since adequate selection and sizing of a frameless motor kit is crucial for a user’s overall robotic joint design, Celera Motion provides online tools and performance prediction software to permit rapid, precise component selection that can help realize any design needs.
.jpg)
Figure 6. Agility Motor Kit
Encoders for the Input and Output
Encoder: Input (Motor) Side of Joint
The motion profile is enhanced by medium-resolution encoder feedback (100,000 to 250,000 counts/ revolution, for example), which enables smooth velocity trajectories. If the motor drive only controls torque, then lower values of resolution are enough. However, velocity and position control are significantly improved with higher resolution in this range.
The integrated robot joint in Figure 1 utilizes an optical encoder kit able to perform over 200,000 counts/revolution, with installed accuracy of 20-50 arc-seconds. It is a low-profile, diffraction-based, interpolated encoder which utilizes a glass grating.
Optical encoders conventionally embody higher precision, quantified in arc-seconds, in comparison to alternative lower performance encoder technologies such as magnetic and capacitive encoders, which are quantified in arc-minutes. Although high accuracy on the input might not seem to be as important, it can affect performance. For instance, if the control system differentiates a position to generate a velocity signal, inaccuracy in the position information will generate a velocity ripple.
Figure 7 below depicts a Celera Motion Optira™ Series configured as a medium-resolution, low-profile, optical encoder kit comprising a read head and glass grating. This kit utilizes PurePrecision™ technology and can achieve resolution of 250,000-500,000 counts/revolution and accuracy in the 20-50 arc-seconds range. This is around two to five times more accurate than magnetic encoders or resolvers. The kit also offers medium resolutions and allows for higher motor speeds of the input shaft.
The integrated robot joint in Figure 4 utilizes an inductive absolute encoder kit and is able to achieve up to 21 bits (2.1 M counts/rev) of resolution with an accuracy of +/- 65 arc-seconds.
.jpg)
Figure 7. Optira Read Head and Glass Grating Scale
The IncOder inductive encoder series comprises a rotor and stator two-part assembly. Electrical signals undergo inductive coupling between each part to supply position information. Each version includes a large through hole and can undergo straightforward integration with further robot joint mechanical components. The absolute output is available in BiSS-C or SSI protocol.
.jpg)
Figure 8. IncOder Inductive Encoder
Encoder: Output Side of Joint
Motion controllers or robot controllers include algorithms for trajectory control and coordination of multiple robot joints. Such algorithms are dependent on high-resolution feedback at all joints; resolutions more than one million counts/revolution, for example.
The output encoder is one of the most critical components of the integrated robot joint. The performance and precision of the robot are highly dependent on the absolute precision of every joint. In certain instances, the robot controller might rely on the output encoder as a means of compensating for stiffness and deflection of all the joints working together, as well as alterations in environmental variables such as temperature.
The Optira™ Series encoder is also configurable as a high-resolution, high-precision read head using the same grating. It utilizes Celera Motion PurePrecision™ optical technology. In rotary form, such encoders can achieve < +/- 2 arc-seconds of accuracy and resolutions in the tens of millions of counts/ revolutions. Interpolation for digital output is integrated into this compact package, while there is also an option for 1-volt pp sine/cosine output for interpolation in the host controller.
The inductive encoder strategy utilizing IncOder technology provides high-accuracy absolute feedback, covering a broad temperature range and operating with industrial ruggedness in shock and vibration environments — the chosen option comprised a BiSS-C serial communications interface for absolute position feedback.
Motor Control Electronics Integration
Robot joints embodying integrated motor control electronics offer significant benefits regarding usability, reduced wiring expenses and EMI. Nevertheless, this sector is also the most exacting in terms of electronics, since they need to withstand high temperatures, vibrations and dust or heavy magnetic fields.
Locating the appropriate motor controller is not always straightforward. Most off-the-shelf controllers available on the marketplace have been engineered for industrial purposes. The role of this class of servo drive is to cover as many possible feedback types and communication busses, rendering them applicable to most applications. However, this also comes with downsides, particularly for integrated robot joints.
.jpg)
Figure 9. Integrated Robot Joint with Everest Series Servo Drive
- General-purpose architectures utilizing DSP and FPGAs cause the heat produced by the electronics to increase.
- Servo drives calibrated for industrial machines, for which trajectories are pre-planned, do not prioritize communications latency.
- A compact industrial servo drive is still far larger than what is necessitated for integration inside a robot joint. Weight can be dramatically increased in comparison to servo drives for motor integration.
Everest Series servo drives for integrated motors are engineered and produced using cutting-edge technology, enabling them to offer the lowest standby power dissipation, in addition to optimized DSP technology, which allows high positioning accuracy. This is the solution presented in Figure 9, wherein the off-the-shelf servo drive has undergone integration inside the robot joint.
Most robots implement safety functions in accordance with torque feedback from the robot joint. By evaluating the torque exerted by the robot joint, the force that the robot arm can exert on a patient or user near the machine is managed to prevent it from harming anybody.
The most regular application comprises the utilization of a motor controller capable of reading torque sensors and feeding the information back to the master controller via the real-time, deterministic EtherCAT bus. In Figure 10, a series of safety mechanisms were applied utilizing an Everest NET plug-in servo drive and a bespoke interface board:
- Motor controller torque input is fed back to the master controller over the EtherCAT bus.
- The system comprises dual BSS-C encoders and digital halls for redundancy. Whenever there is a mismatch between the encoders, the servo drive informs the master controller.
- The motor controller comprises Safe Torque Off functionality, causing the power stage to be disabled following activation.
.jpg)
Figure 10. Collaborative Robot Axis Joint with Integrated Safe Electronics
Power Density
When conceptualizing robotic axis joints, one of the principal restrictions facing mechanical and electronics engineers is the difficulty of locating components with enough power density, the correct form factor and low-heat dissipation.
The utilization of novel, non-silicon-based transistors comprising cutting-edge gate driver technology enables the Everest Series to offer power densities reaching 0.21 W/mm3. This high-power density permits the integration of motor controllers on the end of arm effectors for surgical robots or humanoid robot wrists and fingers. However, size is one of many factors that need to be considered when engineering integrated robot joints. To enable the integration of a motor controller inside a robot joint, heat also needs to be appropriately regulated. The flexible architecture permits high-performance and low-heat dissipation with standby power consumption reduced to 2.5 W.
Mechanical Housing and Output Shaft Components
The overall form factor of a robot joint is governed by general robot operational needs. In Figure 2 and Figure 4 above, the housing comprises three sections. There are two shafts: one internal for the motor and input encoder, and one external for the gear output and output encoder. Each part is accurate, conforming to guidelines of the bearing, encoder, and motor suppliers.
Housing design should account for the following:
- Relative accuracy of the housing needs to match the bearing, motor, and encoder requirements.
- High resolution encoders necessitate particularly tight axial and radial runout specifications. Any runout will lower absolute accuracy. It is usual to utilize ABEC 7 or better bearings.
- Material selection must achieve both mechanical precision and compensate for temperature fluctuations.
- In the case of a robot joint, weight is critical, and thus reducing the number of parts is recommended.
Conclusion
In this technical case study, the most compact, lowest profile robot joint is engineered with a combination of low-profile gearing, optical incremental or inductive absolute encoders, direct drive frameless motor kit, brake, and integrated drive control electronics. This design path includes the lowest quantity of components, offering the highest torque output in the smallest axial length. Although the eventual external packaging will vary according to application, the internal components of the integrated assembly presented above are shared, and the broad approach can benefit all sections of the robotics market.
Every robot joint possesses a set of conditions, including voltage and current inputs, torque and speed requirements, and temperature limits on the interior and exterior of the assembly. It is critical to consider electrical, thermal, and mechanical integration of every component, in addition to the manufacturability of the whole assembly.
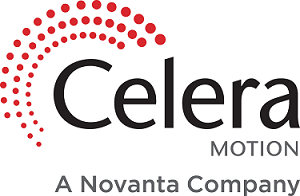
This information has been sourced, reviewed and adapted from materials provided by Celera Motion.
For more information on this source, please visit Celera Motion.