Article Updated on 7 May 2021
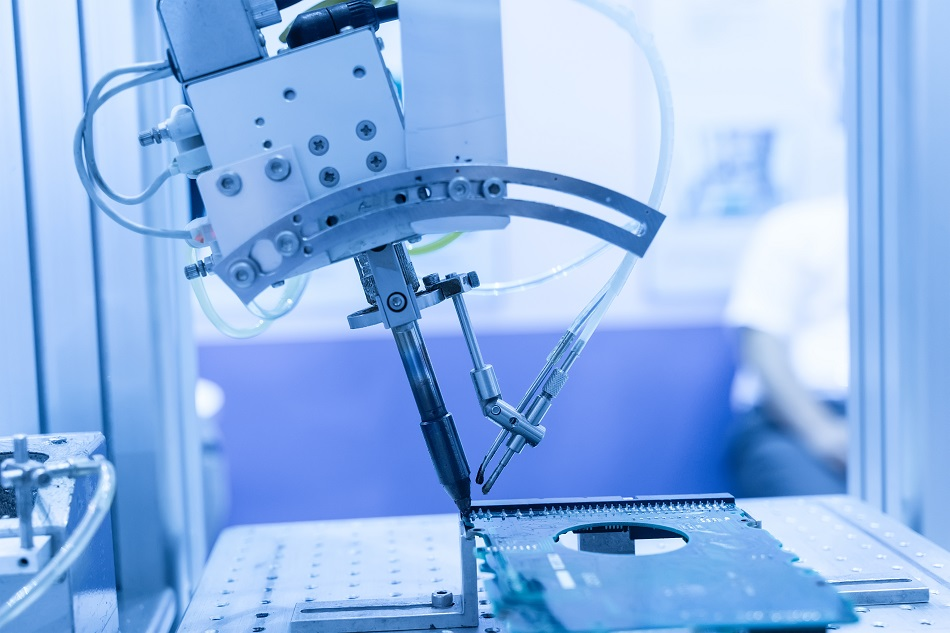
Image Credit: asharkyu/Shutterstock.com
There are various methods of measuring thin film thickness utilizing industrial robotic systems, but the accuracy can vary. Being able to measure the thickness is essential in modern society due to the wide application of thin films.
Thin films are used to coat optical sensors, engine parts, semiconductor devices, and thin-film photovoltaics. Photovoltaics are widely used in the production of the most common solar panels, so having the ability to measure thin film thickness is important.
Methods
One of the most common methods is Ion Beam Analysis using a Rutherford Backscattering technique (RBS). The advantage of this method is that it requires no sample preparation and analysis takes a matter of minutes.
The results are absolute and do not require sample-matched standards or any other assumptions about the sample. RBS enables analysts to detect film roughness along with things like contamination.
Heavy Ion Elastic Recoil Detection (HI-ERD) is also commonly used. Similar to RBS, it looks at the results rather than the scattered particle using a heavy ion beam with recoil artificial intelligence.
Other methods including Ellipsometry and Profilometry are not as accurate as RBS. Ellipsometry relies on the model being used for interpretation.
Profilometry is direct and sensitive (it can measure less than 10 nm film thickness) but it can only measure the location of the step. This means one has to depend on the film being uniform, which it often isn’t. Profilometry also forces an assumption on the density of the thin film, resulting in analysts being misled by oxidation or contamination.
The Robots
The measurement of thin films heavily relies on the ability to detect and measure the light spectrum.
A microspectrophotometer used by CRAIC systems, can detect film thickness by utilizing spectrophotometric measurements in reflection or transmission. The best way to explain its operation is to take the example of looking at oil in water.
The colors of the rainbow are reflected on the surface, due to light being reflected from the top and bottom surface of the oil (oil-air and oil-water interface).
Depending on the film thickness and the angle in which it is observed, the colors will change and one of them can be seen at a particular point. When the angle of observation moves, the color will change.
The microspectrophotometer can measure the colors in transmission or reflection, resulting in an interference pattern in the spectrum. The thickness of the film can then be calculated with a high degree of accuracy.
Another robotic system used to measure thin film thickness is the Materials Acceleration Platform (MAP). Part of a Self-Driving Robotic Platform, MAP can analyze and optimize thin films used commonly in energy conversion, storage, and energy conservation technology.
MAP works by being able to modulate the optical and electronic properties of thin films by changing the film composition, deposition parameters, and annealing (heat treatment) conditions. MAP is a highly sought-after platform due to its mobility.
Thin-film measurement is also widely used in the automotive industry. It is used to help engineers in measuring the correct thickness of vehicle surface paint and mechanism protective layers. Knowing the thickness of film coatings is essential to improve efficiency and durability.
With many vehicles having primers of less then 40 microns (0.04 mm), automated robotic systems are an essential tool in the construction process. The robotic PELT system is an automated online coating thickness management system used in assembly plants around the world.
The system is equipped with multiple sensors, enabling it to provide accurate data across 16 channels of measurement. This provides engineers with a continuous stream of online coating thickness data, allowing them to calculate the exact proportions of film needed to coat the surface of a vehicle.
Industrial robots have made it possible to accurately measure thin film thickness, but also to apply this data in a beneficial way across multiple sectors including automotive, energy conservation, and medicine.
Sources and Further Reading
Disclaimer: The views expressed here are those of the author expressed in their private capacity and do not necessarily represent the views of AZoM.com Limited T/A AZoNetwork the owner and operator of this website. This disclaimer forms part of the Terms and conditions of use of this website.