By automating intricate tasks such as inspection, analysis, and repairs, robots ensure turbine uptime, preempt potential issues through predictive maintenance, and ultimately contribute to lower operating costs while propelling renewable energy generation to drive sustainability objectives.
The global significance of wind energy has led to the rapid increase in wind farms worldwide, with over 400,000 turbines generating nearly 600 GW of power. Ensuring the efficient operation of these turbines is crucial, as annual maintenance is essential but can elevate the overall cost of ownership and impact their competitiveness compared to traditional power sources.
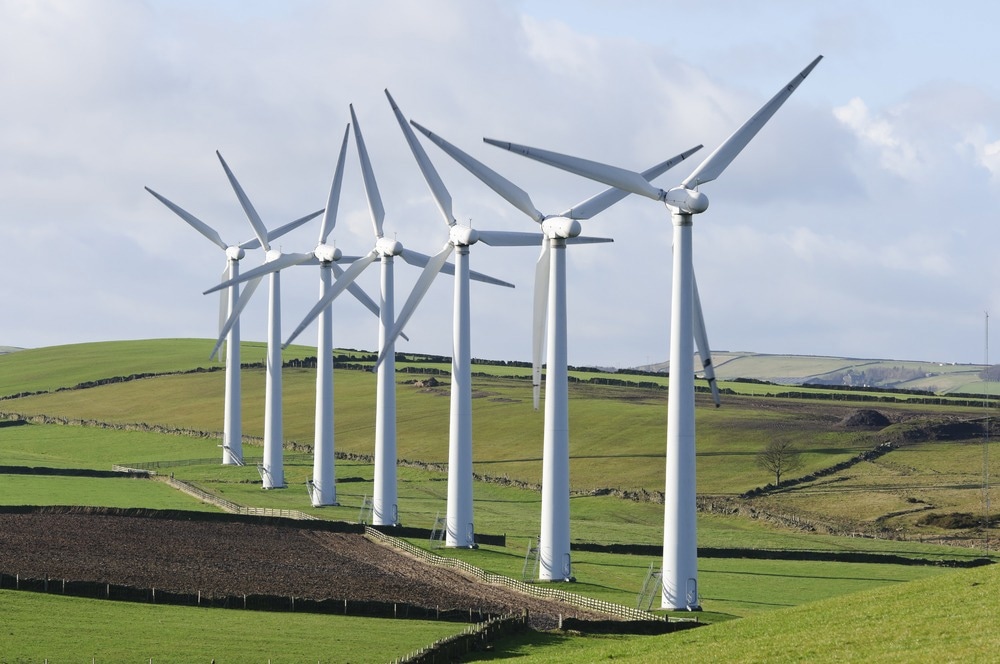
Image Credit: Steve Meese/Shutterstock.com
While wind turbine technology has evolved, maintenance challenges persist for components such as towers and rotor blades, which demand regular and meticulous attention due to harsh weather conditions and their substantial size.
To address these challenges, robots and autonomous systems are emerging as transformative solutions for wind farm maintenance. Robots with high-resolution vision sensors perform remote inspections of challenging spots like turbine blades for thorough cleaning, inspections, and repairs, enhancing safety, minimizing downtime, and improving maintenance quality.
Adopting robotic technology allows wind farm operators to transition from manual inspections to predictive maintenance, using digital twins and sensor data for efficient, long-term condition monitoring.
As the global renewable energy capacity continues to expand, the reliance on robots for wind farm maintenance is expected to grow, ensuring these vital clean energy sources remain operational, safe, and cost-effective.
Commercial Robotic Solutions Minimize Turbine Downtime
A UK-based company introduced the wind turbine inspection robot "BladeBUG," which completes inspections in 35 minutes, half the time of manual methods, offering a swift, secure, and cost-efficient alternative to rope-access technicians.
The robot is tethered to a ground-level rope lowered from the turbine's top, enabling it to be hoisted into position for inspection. The approach is particularly suitable for offshore turbines, saving time by avoiding transporting the robot to the turbine's top.
The robot's founder, Chris Cieslak, emphasized its autonomous capability to perform bolt checks independently, enhancing wind turbine maintenance safety and cost-effectiveness.
Aerones, a Latvian startup, has serviced over 300 turbines in 17 countries with remote-controlled robots that clean and inspect blades. The robots clean towers and blades using liquid detergent, collect leaked oils and repair damaged areas using ultrasound scanning cameras for precise restoration.
Aerones claims its robotic system can increase annual energy production by 12% by minimizing turbine downtime.
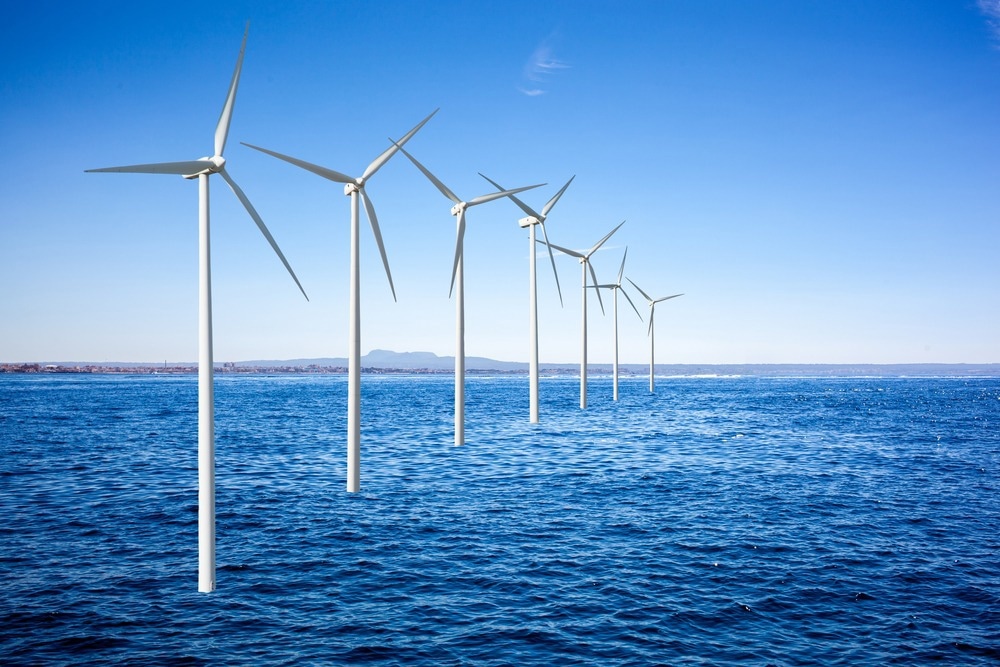
Image Credit: artjazz/Shutterstock.com
Underwater Robots for Offshore Wind Industry
Researchers at the Technical University of Denmark (DTU) are developing an innovative modular robot to inspect and maintain offshore wind turbines.
The initial focus is on inspection and monitoring tasks, such as assessing the condition of underwater wind turbine foundations. As the robot evolves, the plan is to incorporate multiple independent modules capable of collaborative and individual work, including foundation repairs.
The modular robot excels in sensor installation, easily installing and replacing sensors in underwater docking stations on wind turbine foundations. This feature allows continuous monitoring and permanent underwater installation, ensuring consistent operation regardless of weather conditions.
Project UNITE Deploys Remote Robots to Inspect U.K.'s Offshore Wind Farms
Researchers from National Robotarium in Edinburgh are developing underwater robots to remotely inspect and repair offshore wind turbines. Partnering with geo-data specialist Fugro, this £1.4 million initiative, known as the Underwater Intervention for Offshore Renewable Energies (UNITE), aims to enhance worker safety by reducing hazardous offshore missions.
The project focuses on remotely operated robotic systems, addressing challenges in carbon reduction, improved turbine productivity, and cost-effective maintenance.
With over 11,000 offshore wind assets in the U.K., each requiring regular check-ups, the project aims to replace manual inspections with autonomous and semi-autonomous ROVs, contributing to the growth of the offshore renewable sector and the broader net-zero emissions target.
Rope Robotics' Blade Repair Robot Pays for Itself Within Six Months
Rope Robotics' patented robot "BR-8" has been operating for over 18 months, repairing more than 150 turbine blades affected by rain erosion across the United States, Canada, South Africa, and Europe.
The system's core is a robot equipped with visual sensors, using a flexible arm to operate repair tools while technicians oversee operations remotely or on-site. The robot, weighing 150 kg, attaches to ropes anchored in the nacelle, allowing it to reach damaged blades. It inspects the blade using a high-resolution camera and laser scanner, transmitting real-time images to remote operators who guide the repair process.
The repair process includes three phases—sanding damaged areas, cleaning surfaces, and applying protective material—executed precisely by the robot under remote technician supervision, ensuring consistent quality.
The BR-8 robot restores up to 3% energy output per blade within a day, at half the cost of manual methods, showcasing quick return on investment (ROI) for turbine owners.
Feedback from customers so far confirms our calculations that after six months, the investment in the robot repair service has paid off. The robot has been well received especially in countries like the U.S. and South Africa where there has been a backlog of repairs. The robot is therefore an additional capacity to the market right now.
Martin Huus Bjerge, CEO, Rope Robotics
Sandia's Crawling Robots and Drones Provide Comprehensive Turbine Assessments
As wind turbine blades grow larger and more complex, the challenges of inspecting and maintaining them have intensified due to their exposure to environmental elements like lightning, rain, and hail. In response, Sandia National Laboratories has pioneered advanced robotic and drone technology to revolutionize this process.
The technology includes a crawling robot that non-invasively scans and inspects the blade's internal structure and drones equipped with infrared cameras and lidar for thermal imaging and high-resolution analysis.
This combination enables non-invasive inspections, revealing hidden damage and ensuring precise erosion tracking on wind turbine blades, promoting longevity, safety, and cost-effective maintenance through early issue resolution.
Future Outlook
As the technology matures, robots are set to take on progressively intricate tasks, including remotely automated turbine repairs, leading to optimized energy production. Robots and drones equipped for blade cleaning and predictive maintenance systems driven by robotic inspections will proactively address potential issues, bolstering operational reliability.
Embracing robotics is destined to redefine wind farm maintenance, enabling unprecedented levels of efficiency and sustainability while solidifying their role in driving down costs and maximizing renewable energy generation.
References and Further Reading
Aiswarya PM. (2023). Robots minimize downtime on wind turbines by cleaning and inspecting without the help of human workforce. [Online]. Available at: https://www.analyticsinsight.net/robots-to-minimize-downtime-on-the-wind-turbines/
Chong, Z., Xie, F., Liu, X. J., Wang, J., & Niu, H. (2020). Design of the parallel mechanism for a hybrid mobile robot in wind turbine blades polishing. Robotics and Computer-Integrated Manufacturing, 61, 101857. https://doi.org/10.1016/j.rcim.2019.101857
Franko, J., Du, S., Kallweit, S., Duelberg, E., & Engemann, H. (2020). Design of a multi-robot system for wind turbine maintenance. Energies, 13(10), 2552. https://doi.org/10.3390/en13102552
Froese, M. (2017). DTU's new research lab to develop underwater robots for offshore wind industry. [Online]. Available at: https://www.windpowerengineering.com/dtus-new-research-lab-develop-underwater-robots-offshore-wind-industry/
Jake, L. (2023). Crewless maintenance vessels to support offshore wind farm repairs. [Online]. Available at: https://thenationalrobotarium.com/crewless-maintenance-vessels-to-support-offshore-wind-farm-repairs/
Meub, K. (2019). Don’t set it and forget it — scan it and fix it with tech that detects wind blade damage. [Online]. Available at: https://newsreleases.sandia.gov/wind_robots/
Skyspecs. (2022). Using Robotics and A.I. to Optimize Wind Operations and Maintenance. [Online]. Available at: https://skyspecs.com/blog/using-robotics-and-ai-to-optimize-wind-operations-and-maintenance/
WPED Staff. (2023). Rope Robotics finds its wind turbine blade repairs pay off in six months. [Online]. Available at: https://www.windpowerengineering.com/rope-robotics-finds-its-wind-turbine-blade-repairs-pay-off-in-six-months/
Disclaimer: The views expressed here are those of the author expressed in their private capacity and do not necessarily represent the views of AZoM.com Limited T/A AZoNetwork the owner and operator of this website. This disclaimer forms part of the Terms and conditions of use of this website.