Sep 19 2018
In Snow White and the Seven Dwarfs, the jealous stepmother of the protagonist orders the title character to be killed. Snow White escapes and is later discovered hiding in the seven dwarfs’ cottage. To further her evil agenda, the stepmother disguises herself as a hag to deliver a poisoned apple, which causes Snow White to fall into a deathlike sleep that can only be broken by a kiss from a prince. Here Harel Boren, CEO of Inspekto, founder of Autonomous Machine Vision, explains how manufacturers and their QA managers can ensure their QA story has a happy ending, just like Snow White’s.
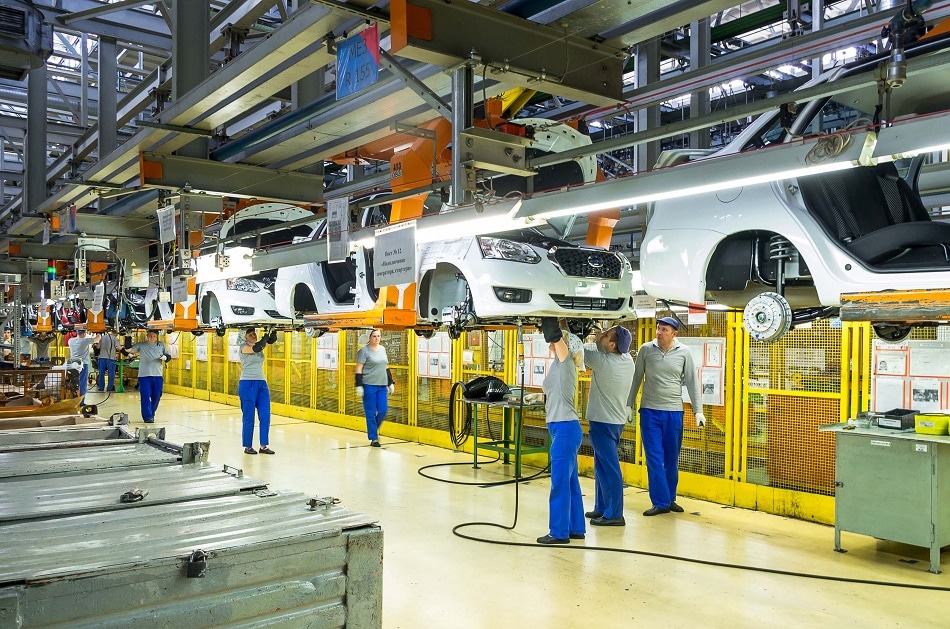
For decades, manufacturers have been the damsel in distress in a much more expensive story; the integration of Traditional Machine Vision. In this tale, visual Quality Assurance (QA), gating and sorting has always been the necessary evil, helping manufacturers reduce the risk of defective products. The process begins with the manufacturer identifying a need for QA and assessing whether a certain point on the production line is worth the time, effort and cost of implementing a machine vision solution.
If it is, the manufacturer will then appoint a systems integrator to put together a QA solution for critical points on the production line. This is because implementing a Traditional Machine Vision solution requires a long process of planning, design and commissioning. This lengthy procedure requires preparing Proof of Concepts, tedious test plans and development of the final applicable solution. To build that inspection solution, the appointed integrator is required to choose an array of lighting, cameras, lenses and other components.
Once a solution has been defined, the integrator will then install it during a period of production downtime ─ an additional cost for the manufacturer. After all this work, you’d expect a consistent and trustworthy, reliable solution, equipped to deal with the challenges of the future. You’d be wrong. What many QA managers discover is that what they’ve actually been given is a poisoned apple.
Twist in the tale
Once a manufacturer has taken this course, they are trapped. Any changes to the conditions in the factory or to the product being manufactured requires the integrator to return to address the problem. In many scenarios, it requires the entire process to be repeated to design an entirely new solution from scratch. The manufacturer is held captive to the machine vision solution installed. In fact, many manufacturers feel they’ve turned out to be a ‘profit centre’ whose difficulties continually feed the systems integrator with more and more work – and more and more budget.
Because implementing a traditional machine vision solution is so complex, it would be impossible for the QA manager or any other staff to complete the task themselves. The manufacturer has never had the choice but to accept the poisoned apple or run the risk of defective products. But this is about to change.
A happy ending
Just like Snow White waited for Prince Charming’s kiss, the market has long been waiting for Autonomous Machine Vision. Developments in image registration, computer-vision, deep learning and other artificial intelligence (AI) technologies have enabled the development of Plug and InspectTM technology required to power a system that gives the QA manager complete autonomy.
Autonomous Machine Vision provides the QA manager with the freedom to install and maintain his or her own systems, because it is straightforward to set up and install. Without any external help, the manufacturer can install and run a system anywhere on the production line and set it up within minutes. What’s more, the system is self-setting and self-learning, which means that when changes are made to the production line, the system self-adapts, so the entire process can be managed in-house.
Because of Autonomous Machine Vision’s affordability and immediacy, it opens up the possibility of Total QA, where machine vision systems are not limited to critical points but can be installed at all stages of the production line. Total QA allows the manufacturer to identify defects as they occur, preventing wasted time and resources.
Autonomous Machine Vision liberates manufacturers from the poisoned apple trap. Instead, manufacturers are free to independently install, by themselves, visual QA systems at all stages of the production line to address defects early on ─ that’s a happy ending if I’ve ever heard one. The spell is lifted for QA managers, allowing them to live happily ever after.