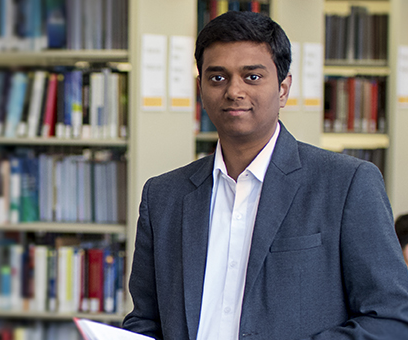
Sharan Srinivas. Image Credit: University of Missouri
This is likely to become a reality earlier than expected, thanks to engineers at the University of Missouri, who are involved in accelerating the online delivery process by creating a software model engineered to make “transport” robots smarter.
Likewise, we have a similar set of questions for the human worker. The most challenging part is optimizing the collaboration plan between the human pickers and robots.
Sharan Srinivas, Study Researcher, Department of Industrial and Manufacturing Systems Engineering and the Department of Marketing, University of Missouri
At present, a huge proportion of labor costs and human effort are involved with achieving online orders. To help enhance this process, robotic companies have already created collaborative robots—also called cobots or autonomous mobile robots (AMRs)—to function in distribution centers or warehouses.
The AMRs are fitted with cameras and sensors to help them move around a regulated space such as a warehouse. The suggested model will help promote faster fulfillment of customer orders by enhancing the core decisions or questions about collaborative order picking, Srinivas explained.
“The robot is intelligent, so if it’s instructed to go to a particular location, it can navigate the warehouse and not hit any workers or other obstacles along the way,” Srinivas said.
Srinivas, who focuses on data analytics and operations research, said AMRs are not engineered to swap human workers but rather to function collaboratively together with them to help boost the effectiveness of the order fulfillment process.
For example, AMRs can help accomplish many orders at a time from separate zones of the warehouse faster than a human worker. However, human workers are still required to help pick items from shelves and position them onto the robots to be moved to a pre-determined drop-off point within the warehouse.
“The one drawback is these robots do not have good grasping abilities,” Srinivas said. “But humans are good at grasping items, so we are trying to leverage the strength of both resources—the human workers and the collaborative robots.”
So, what happens in this case is the humans are at different points in the warehouse, and instead of one worker going through the entire isle to pick up multiple items along the way, the robot will come to the human worker, and the human worker will take an item and put it on the robot. Therefore, the human worker will not have to strain himself or herself in order to move large carts of heavy items throughout the warehouse.
Sharan Srinivas, Study Researcher, Department of Industrial and Manufacturing Systems Engineering and the Department of Marketing, University of Missouri
Going forward, Srinivas stated that their software could also be applied in other scenarios like grocery stores, where robots could be employed to fill orders while also steering among the customers. He envisions this to take place within the next 3-to-5 years.
Details of the study can be found in the International Journal of Production Economics. Shitao Yu, a doctoral candidate in the Department of Industrial and Manufacturing Systems Engineering at MU, is the study’s co-author.
Journal Reference
Srinivas, S. & Yu, S. (2022) Collaborative order picking with multiple pickers and robots: Integrated approach for order batching, sequencing and picker-robot routing. International Journal of Production Economics. doi.org/10.1016/j.ijpe.2022.108634.