Researchers introduced two eco-friendly mobile robots designed using a hybrid analytic network process–interpretive structure modelling (ANP-ISM) methodology.
Their approach demonstrated how the use of energy-efficient materials and processes can support more sustainable robotic design. The study emphasized GR’s potential to reduce environmental impact throughout a robot’s lifecycle.
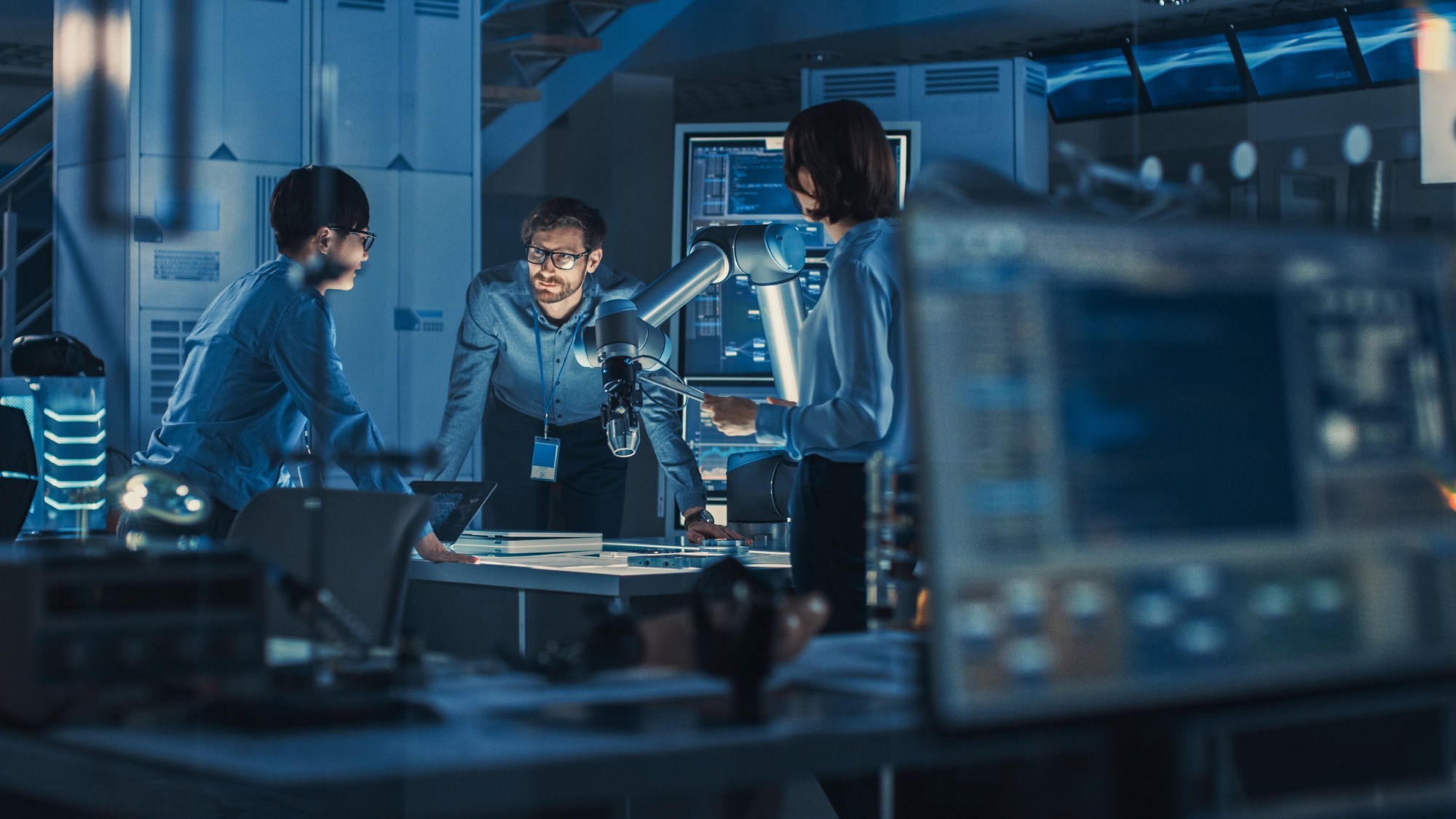
Image Credit: Gorodenkoff/Shutterstock.com
Background
As robotics continues to expand across industries, concerns are growing about the environmental footprint of robot manufacturing and operation. Robotics often relies on energy-intensive processes and materials that are difficult to recycle or degrade.
In other technology sectors, green computing and sustainable supply chains have gained traction, but green robotics is still in its early stages and lacks consistent benchmarks for eco-friendly design.
Past efforts have applied multi-criteria decision analysis (MCDA) to robotic systems, but traditional methods like the analytic hierarchy process (AHP) fall short in capturing the complex, interdependent factors involved in sustainable design. These include energy use, material choices, and environmental impact across a product’s lifecycle.
To address these gaps, the researchers developed a hybrid ANP-ISM approach that considers environmental, economic, and performance criteria. This framework was applied to two types of mobile robots—one for education and one for rescue operations—to show how structured, data-informed design choices can improve sustainability. The model aims to support scalable, eco-conscious development in robotics.
Investigation Procedure
The study used an integrated ANP-ISM methodology to analyze and improve green robot design. The ISM method was used first to establish hierarchical relationships between robot design features.
This process began with a structural self-interaction matrix (SSIM), which was then converted into a binary initial reachability matrix (IRM). After applying transitivity rules, the researchers developed a final reachability matrix (FRM).
From this, they identified levels of influence and dependencies among features. These relationships were visualized using a directed graph (digraph), and MICMAC analysis was used to classify features based on their driving and dependence power.
The second part of the methodology, ANP, evaluated two-way interactions between parameters. Unlike AHP, ANP handles complex network structures and builds pairwise comparison matrices to quantify how different features influence each other. Eigenvalue calculations helped prioritize key elements.
The ANP decision-making process was informed by the ISM’s structural analysis, making the hybrid model capable of addressing the multiple, and often competing, criteria involved in sustainable robot design.
Results and Discussion
The hybrid approach was implemented in two phases. First, ISM modeling used input from 73 experts across academia and industry to map relationships among 14 robot design features. The matrices revealed three feature levels, with programming placed at the highest impact level (Level 3). MICMAC analysis categorized features as either autonomous—critical to system function—or as linkage features, which were less stable in influence.
In the second phase, the ANP process was used to rank design alternatives for two robot examples. For the educational robot (Example 1), the Arduino-based configuration (A1) scored highest when all four criteria—cost, eco-friendliness, energy use, and learning potential—were considered.
When focusing solely on environmental performance, a design using biodegradable components (A9) ranked highest. For the rescue robot (Example 2), the design featuring a metal chassis and direct current (DC) motors (A4) was preferred when all criteria were weighed.
A sensitivity analysis using multi-attribute utility theory (MAUT) confirmed that the recommended choices remained consistent even when weights were adjusted. This demonstrated the robustness of the decision-making process.
The findings showed that the ISM-ANP framework can effectively manage trade-offs in green robotics design. Key outcomes included reduced carbon footprints through renewable energy integration and more thoughtful material selection. These results highlight the practical benefits of applying structured methods to environmental design challenges. The researchers suggest future work could involve artificial intelligence tools to enhance the model and extend its use to industrial-scale robotics.
Download your PDF copy now!
Conclusion
This study showed that the hybrid ANP-ISM framework can help address sustainability challenges in robotics by systematically balancing environmental, economic, and performance goals. When applied to educational and rescue robots, the method successfully guided improvements in material selection, energy use, and lifecycle impact.
The ISM phase revealed the most influential design features, while ANP enabled decision-making that accounted for conflicting objectives. Sensitivity analysis confirmed the stability of these design choices under changing priorities. The approach supports reduced carbon emissions and encourages more sustainable design practices.
As green robotics becomes increasingly important to sustainable technology development, this framework offers engineers a structured model for building more eco-conscious systems, while reinforcing the need for standardized guidelines in the field.
Journal Reference
Sathiya, S, et al. (2025). Designing green robots with environmental sustainability by applying the concept of multi-criteria decision making. Scientific Reports. DOI:10.1038/s41598-025-07605-2, https://www.nature.com/articles/s41598-025-07605-2
Disclaimer: The views expressed here are those of the author expressed in their private capacity and do not necessarily represent the views of AZoM.com Limited T/A AZoNetwork the owner and operator of this website. This disclaimer forms part of the Terms and conditions of use of this website.