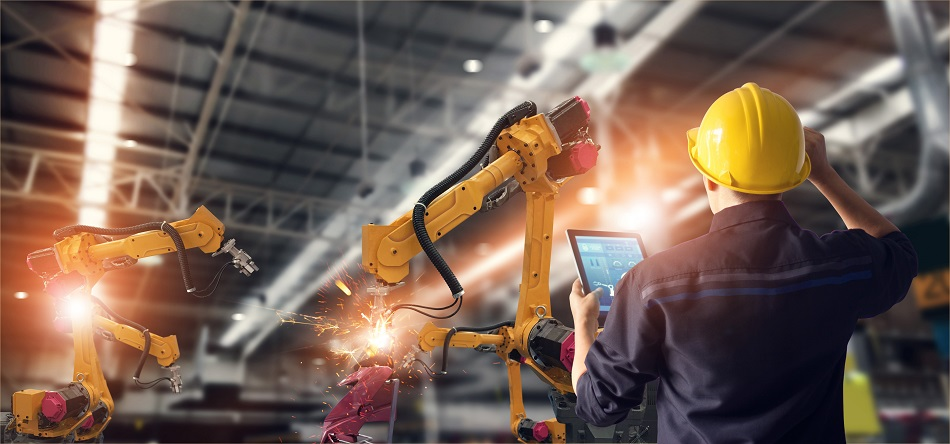
Image Credit: PopTika/Shutterstock.com
Superalloys are metals that can withstand high temperatures without deforming (including creep) or corroding, and usually contain high proportions of refractory alloying agents such as nickel and cobalt (AZoM, 2002).
They also feature excellent mechanical strength, high levels of resistance to oxidation (rust) and other kinds of chemical corrosion, and good surface stability. Examples include Hastelloy, Inconel, Waspaloy, Rene alloys, Incoloy, MP98T, TMS alloys, and CMSX single crystal alloys.
In robotics, these metals are a coveted component material. Due in part to robotic systems often being placed in environments that are too hazardous or otherwise inconvenient for human workers, such as the extreme heat of some industrial processes, excessive radiation in the case of nuclear energy generation, long periods of submersion under the sea or even the extreme cold, and winds in space missions.
Robotics also utilizes superalloys to ensure robustness and durability (known as ruggedization) for robots used in the high-impact operations of industries like mining and manufacturing or to complete a diverse array of tasks in the hazardous situations of disaster relief or military applications. With superalloy-based components, robots can be designed to withstand years of productive operation in tough environments.
Hastelloy
Hastelloy is a brand name for superalloys which resist extremely high levels of corrosion. It is produced exclusively by Haynes International in their plants in Indiana, Louisiana, and North Carolina, United States. Most Hastelloy alloys are nickel-based, but cobalt, chromium, molybdenum, tungsten, iron, silicon, manganese, carbon, aluminum, and titanium are also used.
Due to its corrosive-resistant properties, Hastelloy is used in robotic sewer maintenance systems. These robots must withstand high levels of chemical and water corrosion, and perform tasks in areas that are hard to access for human recovery workers. Therefore the superalloy components have to be highly ruggedized, and Hastelloy is a good choice for this kind of robot application.
Incoloy
Incoloy alloys are produced in the United States by Special Metals Corporation, headquartered in New York. They are typically based on nickel and are designed to withstand extreme temperatures of hot and cold. They also have excellent corrosion resistance properties.
Due to their good resistance to temperature deformation, Incoloy alloys are frequently used as component materials for thermostats which need to withstand extreme temperatures. In robotics, these ruggedized thermostats are applied in industrial and manufacturing safety monitoring situations where other kinds of thermostat would fail, such as in semiconductor manufacture.
MP98T
SPS MP89T is an alloy used to manufacture specialist fasteners by United Titanium in Ohio, United States. MP98T fasteners have a minimum tensile strength of 180 ksi and fracture toughness that exceeds 200 ksi in. - 1/2. Therefore, they are highly sought after in the aerospace industry and any industry (including robotics) that requires extremely tough fastening components.
Robotics Used in Superalloy Manufacture
Interestingly, there is a significant level of cross-disciplinary cooperation between robotics and superalloys materials science. As well as being used as component materials for robots that require extensive ruggedization as is the case in a submarine, aerospace, disaster relief, and military occupations, modern superalloys require robot assistance for their manufacture.
Due to their high-temperature resistance, many superalloys are very difficult or impossible to weld conventionally. They require far greater temperatures than conventional metals to become weldable, and this is highly dangerous for human workers. As such, robotic laser welding has been developed to automate this process and make manufacturing superalloys safer.
Another robot application in superalloy manufacture is in deburring. Superalloys in the aerospace industry – which accounts for the majority of superalloy consumption today – must be flawlessly deburred or risk causing a potentially life-threatening structural or mechanical failure. This is often performed automatically by robots, who can achieve a more homogenous surface than in conventional methods.
Sources and Further Reading
Disclaimer: The views expressed here are those of the author expressed in their private capacity and do not necessarily represent the views of AZoM.com Limited T/A AZoNetwork the owner and operator of this website. This disclaimer forms part of the Terms and conditions of use of this website.