A large part of my work is inspired by the desire to understand insect flights and the associated physics at the insect scale. When I was an undergraduate student at Cornell University, I was intrigued when studying high-speed videos of fruit flies. Their flight mechanism is drastically different from existing aerial robots, and their agility and robustness far outperform robots.
Building at-scale robots allow me to investigate centimeter-scale flapping-wing physics unique in insects. Furthermore, I am thinking about achieving insect-like functions in future robotic systems, which may enable the exploration of highly cluttered spaces, assisted pollination, etc.
What are dielectric elastomer actuators (DEAs), and do they have any limitations?
DEAs are a type of soft actuator that uses electrostatic stress to induce actuation. We can think of a DEA as a soft capacitor.
There are two compliant electrodes that sandwich a soft dielectric material. When a voltage difference is applied to the two electrodes, electrostatic stress squeezes the elastomer and causes the actuator to change its shape.
Our DEAs exhibit high actuation bandwidth (>500 Hz) and power density (>1 kW/kg), and long lifetime (>2 million cycles), representing the best-in-class performance. DEAs are limited, however, by their high driving voltage (>500 V) and low efficiency (10-20%).
How have you adapted DEAs so that they can be incorporated into an areal robot that demonstrates high performance?
Traditionally, DEAs’ bandwidth is low (<100 Hz), which implies they have insufficient power density to enable flight. We advance the design and fabrication of DEAs by substantially improving their bandwidth.
Specifically, we study how actuation bandwidth depends on electrode resistance, elastomer viscoelasticity and DEA geometry. Having high bandwidth DEAs implies that soft actuators have sufficient power to enable flight.
Next, we design a new aerial robot consisting of new transmission, airframe, wings and wing hinges. These components are designed around the DEAs’ properties.
According to your research, your robot demonstrates the longest, best-performing flight among other existing aerial robots. How did you go about achieving this?
Achieving the longest and best-performing flight among sub-gram aerial robots stems from three properties of the DEAs: good controllability, long lifetime and high output power.
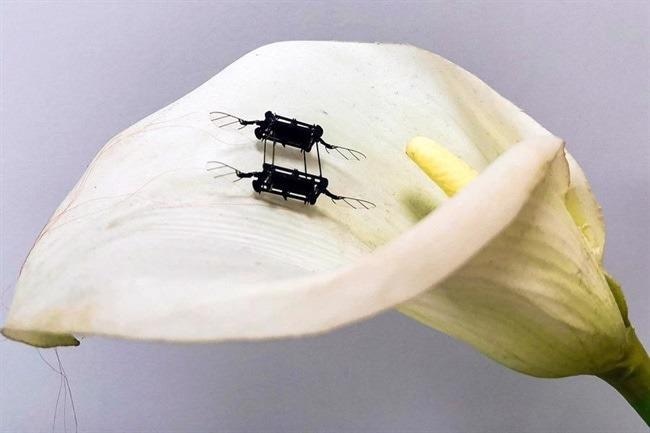
Image Credit: Zewe, A., (2022) Giving bug-like bots a boost. [online] MIT News | Massachusetts Institute of Technology. Available at: https://news.mit.edu/2021/micro-robots-artificial-muscles-1216
Having good controllability means that the DEA can respond to change of control signals quickly, which means the robot can reject disturbances quickly. Having a long lifetime means the DEAs can support flight for a longer time. Finally, having high output power means the robot can generate high lift forces. This means the robot will have enough forces for generating flight torques, which are necessary for control.
How does your new fabrication technique help advance the capabilities of conventional artificial muscles?
The new fabrication techniques we have developed are broadly applicable to most dielectric elastomer actuators. They lead to two performance improvements: a large reduction of actuation voltage and an increase of net energy density and power density.
Insect-like robots
Video Credit: Massachusetts Institute of Technology (MIT)/YouTube.com
We reduce actuation voltages (from 2 kV to 500 V) by developing thin (~10 um) elastomer films. We increase net power density by pulling vacuum to reduce the number of defects in the elastomer film. These improvements enable the robots to operate at lower voltages and deliver higher energy and power.
Can you explain how your muscle-like actuators were made and how they work?
DEAs are made of spin coating, electrode transferring and multiple-layering methods. First, a thin layer (10 um) of elastomer is spin-coated on an acrylic template. It is then put into a vacuum to remove defects and then baked at 60 degrees Celsius for five minutes.
Next, a carbon nanotube electrode is transferred onto the elastomer sheet through vacuum filtration and stamping. This whole process is repeated 20 times to make a 20-layer composite.
Finally, the composite is removed from the elastomer laminate and manually rolled into a cylindrical DEA. Half of the electrodes are connected to a negative terminal, and the other half are connected to a positive terminal.
During actuation, a 400-500 Hz sinusoidal high voltage (500-600 V) signal is sent to the DEA. It causes the DEA to elongate and contract at the actuation frequency (400-500Hz). It is this elongation and contraction that drives the flying robot.
How did you test the efficacy of your artificial muscle, and what were the results of your findings?
We tested the efficacy of the DEAs by measuring the peak-to-peak displacement and blocked force at different driving frequencies. These helped us to calculate the net output power. In addition, we calculated the input electrical power by measuring the voltage and current from the supply. We can calculate the DEA transduction efficiency by knowing the input and output power. The efficiency was estimated to be 12%.
In addition, other performance metrics for this 0.1 g actuator include maximum blocked force (0.35 N), maximum displacement (1.2 mm), bandwidth (500 Hz), and lifetime (>2 million cycles of actuation).
How do your soft actuators compare to more rigid robots?
The performance of our soft actuators (such as output power, force and motion) is similar to the best rigid actuators at this scale (piezoelectric actuators). It is advantageous in the sense that it is easier to fabricate and robust to external disturbances such as collisions.
This makes it particularly suitable for driving robots that may frequently collide with obstacles. However, the current limitation is that it requires higher driving voltage (500 V vs 200V) and has lower efficiency (12% vs 80%).
Do you think that the performance of soft actuators could eventually overtake state-of-the-art rigid ones?
I think both types of actuators will find suitable applications because of their unique advantages. For instance, soft actuators are low-cost and robust, while rigid actuators are precise.
I think the two types of actuators will complement each other in future robotic systems. We envision building hybrid soft-rigid robots – systems that consist of both rigid and soft actuators and other elements, including transmissions and end effectors.
Did you come across any challenges or limitations during your research?
There are a lot of challenges that we had to overcome during our research. The predominant challenge was the limits on low bandwidth and the requirement of high voltages.
Currently, we are working on autonomous soft robots; and this implies we need to build low-weight power sources (batteries) and power electronics (boost circuits) for these systems. My team is developing high voltage and low weight circuit components for future soft robotic systems.
What are the potential applications of these next-generation animal-like soft actuators?
There are three potential applications for these soft actuators. In the short term, we can use small animal-like robots to inspect cluttered spaces. For instance, we can deploy small crawling robots inside a turbine engine to inspect cracks on a turbine blade.
In the mid-term, we can use insect-scale flying robots for assisted pollination in indoor farming applications, and in the long term, we can use a swarm of autonomous insect-scale robots to collectively conduct search-and-rescue missions.
What are the next steps for your research?
We are pushing on two fronts: to develop nonlinear dynamic models of DEAs to enable new flight capabilities in our robots (such as landing on flowers and leaves, following complex trajectories, and flight in a swarm); and to develop lightweight power electronic circuits so future robots can carry their own power sources during flight.
About Kevin Chen
Kevin Chen is currently the D. Reid Weedon, Jr. ’41 Career Development Assistant Professor at the Department of Electrical Engineering and Computer Science, MIT, USA. He received his Ph.D. in Engineering Sciences at Harvard University in 2017 and his bachelor’s degree in Applied and Engineering Physics from Cornell University in 2012. His research interests include developing high bandwidth and robust soft actuators for microrobot manipulation and locomotion. He has published in top journals, including Nature, Science Robotics, PNAS, Nature Communications, IEEE TR-O, and Journal of Fluid Mechanics. He is a recipient of the RAL 2020 best paper award, the IROS 2015 best student paper award, and a Harvard Teaching Excellence Award.
Disclaimer: The views expressed here are those of the interviewee and do not necessarily represent the views of AZoM.com Limited (T/A) AZoNetwork, the owner and operator of this website. This disclaimer forms part of the Terms and Conditions of use of this website.