Oct 22 2012
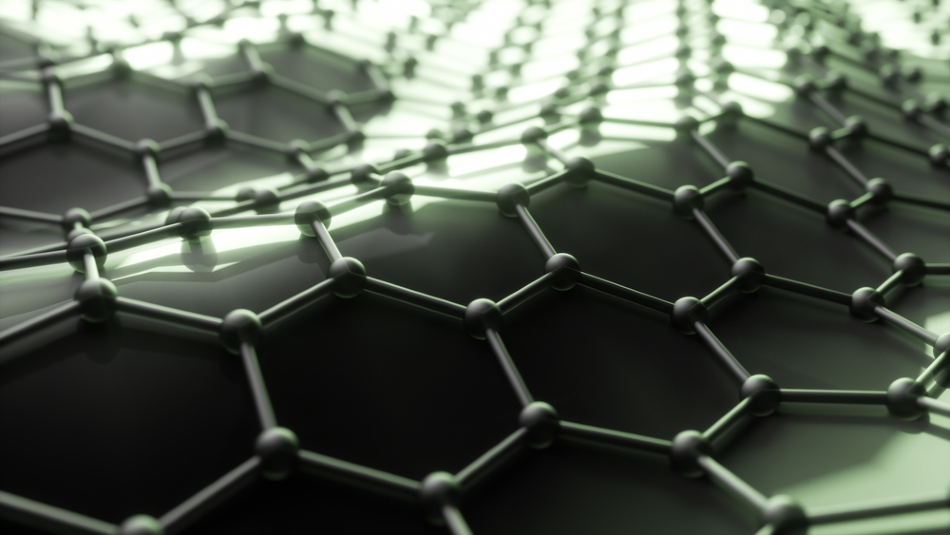
Image Credit: OliveTree/Shutterstock.com
Article updated on 24/02/20 by Mihaela Dimitrova
The study of ferroelectricity can be explained by first discussing polyvinylidene fluoride (PVDF) and its copolymers. Polymer chains of PVDF contain C2H2F2 molecules that have net dipole moments as a result of the electronegative fluorine to hydrogen. These molecules can crystallize with respect to macroscopic polarization. Currently, the solvent-formed ferroelectric polymers in the form of films are produced by casting, stretching and poling or spinning on textured Teflon.
What are Electroactive Polymers?
Electroactive polymers, or EAP, are polymers that change their size and shape when put through electrical stimulation.
Types of Electroactive Polymers
Based on their actuation mechanism and internal qualities, they are classified into:
- Ionic EAPs.
- Electronic EAPs.
Ionic EAPs
The shape of these materials changes with the movement/diffusion of ions and other conjugated substances. Ionic EAPs can function at low driving voltages of about 1-5 V. However, one of the major drawbacks of the utilization of these materials is that they can only operate in solid electrolytes or wet state conditions. Perhaps, ionic EAPs have to overcome the problem of water hydrolysis when operated under aqueous conditions.
Bending actuation produced by ionic EAPs tends to generate lower actuation forces than electronic EAPs. Moreover, in comparison with electronic EAPs, ionic EAPs show slow response. Also, the amount of deformation of ionic EAPs is greater than that of electronic EAPs.
Some of the major ionic EAPs include the following:
- Carbon nanotubes.
- Ionic polymer-metal composites.
- Conducting polymers.
- Ionic polymer gels.
Actuations produced by conducting and gel polymers are mainly through ion/mass transportations.
Electronic EAPs
Electronic EAP materials work through an electric field. They are operated at high activation fields of more than 150 V/μm, which is more or less close to the material’s breakdown level. These materials find their application in robotics as they can sustain induced displacement upon the application of DC voltage. They have fast response time and high energy density.
Some of the major electronic EAPs include the following:
- Liquid crystal elastomers.
- Ferroelectric polymers.
- Electro-viscoelastic elastomers.
- Electrostrictive graft elastomers.
- Electrostrictive paper.
- Dielectric EAP.
Dielectric elastomers produce actuation by means of polarization. Liquid crystal elastomers, on the other hand, produce actuation based on phase change,
Use of Electroactive Polymers for Robotic Application
Research shows that the performance of electroactive polymers as actuators is better than that of the human muscle, which makes them suitable for robotic applications. EAPs play a major role in developing electronic artificial muscles for robots.
Some of the artificial muscles include the following:
Dielectric Elastomers
In this actuator, the elastomer and electrodes are highly compliant. The electrodes used in this actuator function by expanding and contracting with the elastomers, being incompressible. This process can be operated under high electric fields, for instance, acrylic elastomer VHB 4910.
Electrostrictive Graft Polymers
Flexible polymer backbones are grafted with graft-copolymers, while the crystalline regions are formed by the polar side groups. These regions act as the polarizable moieties for performing physical crosslinking and actuation.
Below is an interesting video by VirtualPoint demonstrating the use of NovaMesh Ventral Hernia Mesh medical device. The device is made from electrospun nanofabric ultra-thin polymer fibers that behave like a graft and are used for clinical application.
The NovaMesh Ventral Hernia Mesh (Nicast), produced by Virtual Point
Carbon Nanotube Actuators
The tensile strength of carbon nanotubes (CNTs) is high, which makes them suitable for a range of robotic applications. CNTs can be easily inserted into any composite material, e.g. super-elastic CNT aerogel muscles, which have an elongation rate of 220% at 80-1900 K.
Conducting Polymers
Conductive polymers are actuated when the counter-ions are taken away by the polymer matrix at the time of electrochemical redox cycling. These polymers expand on the basis of migration of counter-anions from the electrolyte (e.g. polyaniline and polypyrrole).
EAPs are relatively new to the field of robotics but they are found to possess properties that are favorable for actuating synthetic muscles. Further improvements in this technology are required for the utilization of EAPs in robotics and humans as well.
References and Further Reading
- Kim.K.J, Tadokoro.S, 2007, Electroactive Polymers for Robotic Applications: Artificial Muscles and Sensors, Springer.
- Ducharme.S, Physics of Two-Dimensional Ferroelectric Polymers - United States