Across all industries, robots are taking control of processes to improve productivity, resource efficiency, and safety. This is one aspect of a new paradigm for industry conceptualized in the “Fourth Industrial Revolution” or “Industry 4.0” model, in which sectors harness computing, connectivity, and automation technologies to realize these benefits.
Mining is a major industry facing productivity, efficiency, and safety challenges in the twenty-first century. As such, it is beginning to embrace all aspects of the Fourth Industrial Revolution, including robotics.
Ongoing Impact of COVID-19: Accelerating Pre-Existing Trends
As is the case in many other sectors, the impact of COVID-19 on mining was mainly to speed up the rate of adoption and deployment of technologies and processes businesses were pivoting toward anyway. These new technologies and processes are characterized by their application of modern computing, connectivity, and automation technologies to improve productivity, resource efficiency, and worker safety.
The mining industry experienced the major impact of COVID-19 on its supply chains and on-site efficiency. The transportation of materials from the mine encountered difficulties, alongside the transportation of machinery, components, and other resources to the mine.
Implementing lockdown measures and measures to prevent the spread of the virus also considerably impacted on-site efficiency, leading to unpredictable shift patterns for workers and temporary closures of many mines. Mining operations extracting residual resources were highly affected by these circumstances.
As a result, mining companies sped up development cycles or embarked on urgent implementation projects for robot technologies that could enable operations to continue safely and practically.
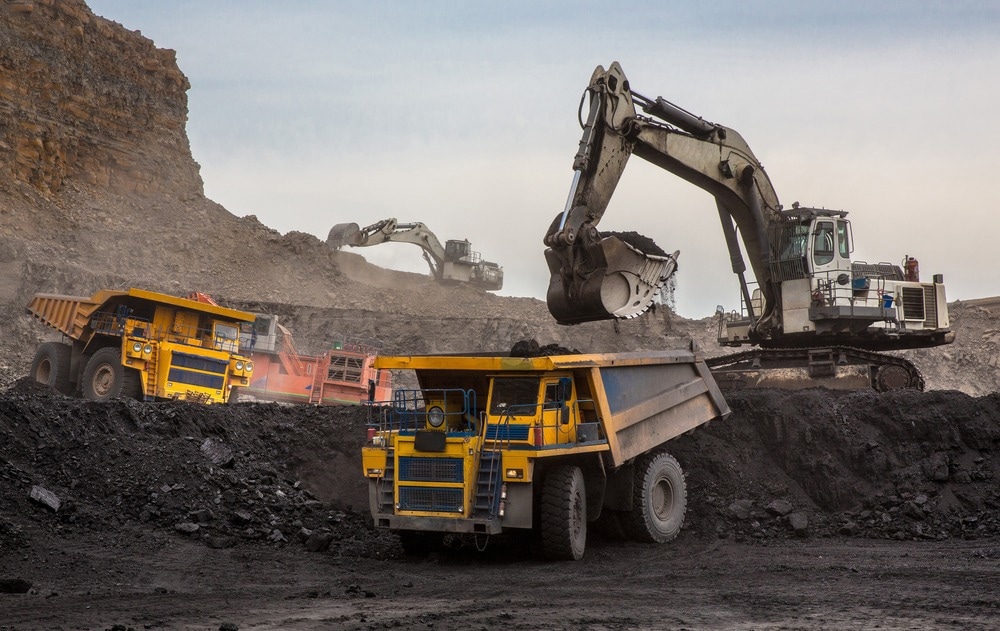
Image Credit: 1968/Shutterstock.com
Robot Diggers
Robotic technology has been applied to mass excavation in mining since the mid-1990s, particularly in surface mining with large hydraulic and electric shovels.
The biggest challenge is the interaction between the tool and terrain, which is influenced by various factors, including media properties, rock pile geometry, and particle size and shape. It is not easy to predetermine interactions before excavation.
Situational awareness, involving workspace and machine awareness, is another challenge for robotic digging. This is typically achieved through a sensor suite on the machine, including ranging sensors, an inertial measurement unit, and a GNSS unit.
As well as digging, autonomous excavation systems also provide real-time survey information and enable dig-to-plan operations.
Robot Dozers
The use of dozers is common practice in most surface mining operations. These machines perform complex duties under dynamic conditions in the presence of variable and subtle hazards that can be difficult to recognize. Proficiency in ground-engaging tool control and machine positioning is imperative for many of these tasks, and as such, autonomous dozers are a technological challenge.
Human dozer operators are exposed to various risk factors that may result in health problems, including whole-body vibrations, awkward postural requirements, noise, and shift work. Although machine guidance systems are now widespread, they still require an operator in the cab and have known issues associated with their dependence on GNSS-based localization.
Mining equipment manufacturers now offer remote-controlled and autonomous dozers, which do not require human operators on board. These technologies can reduce operator exposure to hazardous environments and may also increase efficiency and productivity in surface mining operations.
Robots Improve Safety
The potential of robots to improve mine safety was demonstrated in 2018 when a dangerously over-pressurized water pipe was discovered deep underground in a drill hole at a BHP Nickel West nickel mine in Australia.
BHP enlisted the assistance of Woodside, Deakin University, University of Texas, Clearpath, and NASA robotics engineers to remotely guide a robot through the tunnel to cut the pipe and relieve the pressure. The entire operation, from discovery to resolution, took less than two weeks, and the success was attributed to the use of robotic equipment and safe remote operations.
Underground mines are often subject to accidents resulting from roof collapses and falling debris, leading to worker injuries and fatalities. To address this safety issue, West Virginia University (WVU) engineers are developing an autonomous robotic safety system that uses drones attached to remotely operated ground vehicles to create high-resolution 3D maps of underground mines. The maps assess the pillars and roof for damage, monitor the mine pillars' structural integrity over time, and detect dangerous conditions that could lead to collapse.
Engineers at Queen’s University have also developed new robotic technology to automate loading an underground load haul dump (LHD) bucket with broken-up pieces of rock. This technology improves efficiency and enhances worker safety at the same time.
Robots Enable Remote Operations
Remote connectivity projects in mines worldwide are increasing, allowing companies to streamline production, maximize worker safety, and future-proof mining operations.
Rio Tinto, a global mining company, is leading the way with autonomous operations and robotics projects in Australia. Their iron ore mines operate with a completely autonomous, heavy-haul, long-distance railway system. Over 80 robotic trucks have been deployed in roaming, digging, excavating, and transportation operations at Rio Tinto's Pilbara mine. Only a handful of human workers are left on site to supervise physical operations and provide manual fixes if needed.
To further improve remote operations, Rio Tinto collaborated with the Australian government-backed science organization, CSIRO, to develop a telerobotic control system for the primary rockbreaker at the West Angelas mine. This system addresses known drawbacks in teleoperation, such as limited communication bandwidth and high latency in real-time video feedback, by improving the intelligence of the control system at the remote/machine end and providing the operator with a mixed-reality interface that combines live video with 3D computer visualization.
About 12,000 Rio Tinto employees were relocated to an operations center near Perth Airport, where they work with new skills in the control room 750 miles away from the site.
References and Further Reading
Galas, A., et al (2021). Impact of Covid-19 on the Mining Sector and Raw Materials Security in Selected European Countries. Resources. doi.org/10.3390/resources10050039.
Marshall, J. et al (2016). Robotics in Mining. Springer Handbook of Robotics. dx.doi.org/10.1007/978-3-319-32552-1_59.
Robotic technology promises to improve mining safety. (2015) [Online] Phys.org. Available at: https://phys.org/news/2015-05-robotic-technology-safety.html
Robotics – indispensable tools for the future of mining. (2022) [Online] Mining Technology. Available at: https://www.mining-technology.com/comment/robotics-future-mining/
Pilkington, B. (2021). The Significance of Remote Connectivity in Mining Operations. [Online] AZO Mining. Available at: https://www.azomining.com/Article.aspx?ArticleID=1608
WVU Engineers Utilize Robots to Improve Mine Safety. [Online] West Virginia University. Available at: https://research.statler.wvu.edu/research-projects/wvu-engineers-utilize-robots-to-improve-mine-safety
Disclaimer: The views expressed here are those of the author expressed in their private capacity and do not necessarily represent the views of AZoM.com Limited T/A AZoNetwork the owner and operator of this website. This disclaimer forms part of the Terms and conditions of use of this website.