By Ankit SinghApr 21 2024Reviewed by Susha Cheriyedath, M.Sc.
The manufacturing industry is undergoing a significant transformation thanks to the advancements in robotics and automation. While traditional industrial robots have played a crucial role in automating repetitive tasks, their large size, complex programming, and safety requirements have often restricted their practical application. Collaborative robots, also known as cobots, are revolutionizing the industry, bringing in a new age of human-robot collaboration in the factory setting.
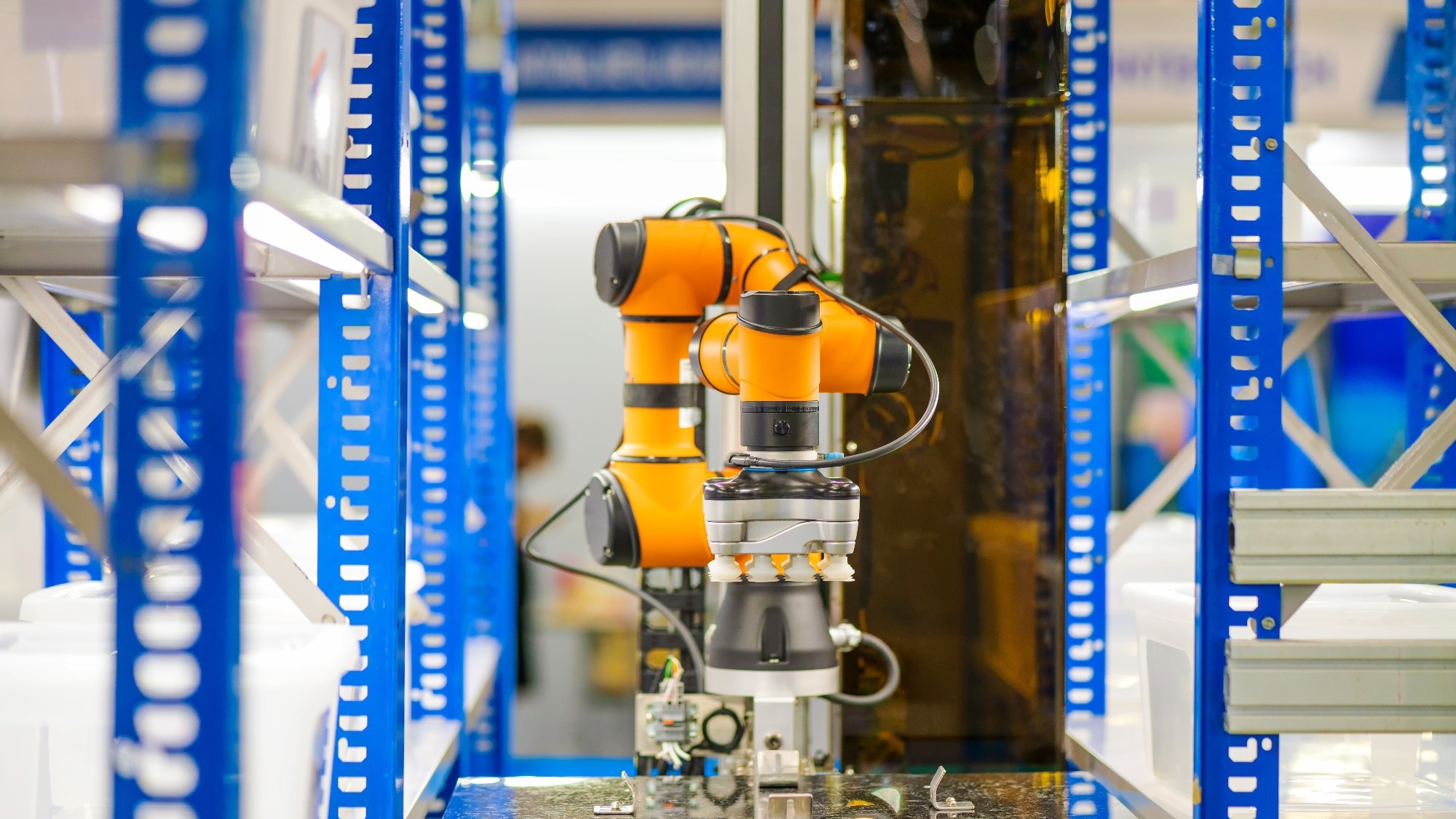
Image Credit: August Phunitiphat/Shutterstock.com
This article explores the evolution, principles, and applications of cobots in manufacturing. It also discusses the challenges associated with their implementation, highlighting the importance of research and innovation in the growth and adoption of cobots.
From Bulky to Buddy: The Evolution and Principles of Cobots
The emergence of cobots can be traced back to the early years of the 21st century. Unlike their industrial counterparts, cobots are designed with utmost precision to enable them to work alongside human workers safely and securely.
Cobots are usually smaller in size, lighter in weight, and are equipped with in-built safety features like force sensors and speed limitations. This unique feature allows them to operate near humans without risk of injury. In addition, cobots are relatively easier to program and deploy, often featuring user-friendly interfaces and programming methods that are easy to understand.1
The principles underlying cobots center around their adaptability and collaborative nature. Cobots complement the abilities of human workers and are not intended to replace them. They excel at performing physically demanding, repetitive, or hazardous tasks, freeing human workers to focus on more complex activities requiring critical thinking, creativity, and problem-solving skills. Moreover, cobots' adaptability enables seamless integration into existing production lines, making them ideal for a broad range of manufacturing applications.2
Beyond Human Reach: Applications of Cobots in Manufacturing
Due to their versatility and ease of use, cobots are becoming increasingly popular in several manufacturing processes. They can be programmed to carry out various tasks and are designed to work alongside human operators safely and efficiently.
Cobots are transforming assembly lines, expertly handling intricate tasks like precision part placement, component assembly, and seamless material feeding. Their lightweight design and maneuverability make them perfect for confined spaces and delicate tasks.1,3
In machine tending, cobots are invaluable, as they can be deployed to load and unload materials from computer numerical control (CNC) machines, 3D printers, and other production equipment. This not only enables continuous operation but also reduces idle time for human workers.4
Cobots can also be equipped with vision systems to carry out quality control and inspection tasks. These systems can identify product defects or inconsistencies and alert human operators to take corrective action. By automating these tasks, cobots can reduce the risk of human error and ensure consistent product quality.4
Lastly, cobots can handle repetitive tasks like packing finished products into boxes or palletizing them for shipping. This not only reduces physical strain on workers but also improves packing efficiency and reduces the risk of injuries. Cobots can also work alongside human operators to perform more complex tasks that require human judgment or dexterity.5
Overall, cobots offer various applications and benefits in various manufacturing processes. They can enhance productivity, improve product quality, and ensure worker safety, all while decreasing costs and downtime.
The Power of Collaboration: Advantages of Cobots
Integrating cobots into manufacturing environments presents several advantages that can have a positive impact on productivity, safety, and overall efficiency. The following is a detailed exploration of some key benefits of cobots in the manufacturing industry:
- Increased Productivity and Efficiency: Cobots are tireless machines that can perform tasks faster and more consistently than human workers. This translates to increased production output, shorter lead times, and, ultimately, a significant boost to overall manufacturing efficiency.1,4
- Improved Worker Safety: Cobots can take over hazardous or physically demanding tasks that pose a potential safety risk to human workers. These tasks may include welding, handling heavy materials, or working with dangerous chemicals. By automating such tasks, cobots significantly reduce the risk of workplace injuries, musculoskeletal disorders, and occupational illnesses, which fosters a safer and healthier work environment for human employees.3
- Enhanced Flexibility and Adaptability: Unlike their traditional counterparts, cobots are relatively easier to program and reconfigure for different tasks. This inherent flexibility makes them an ideal fit for variable production runs, offering manufacturers the convenience of quickly adapting to evolving market demands or product specifications. Cobots can be programmed to handle a wide range of tasks, including assembling a new product or packaging a different size variation. Such versatility provides manufacturers with the agility to adjust their production lines with minimal downtime or extensive retooling.1,5
- Reduced Labor Costs: Investing in cobot technology involves an initial cost for acquisition and integration. However, the long-term advantages, such as enhanced productivity reduced downtime and minimized labor costs, can result in substantial savings over time.3,4
Challenges and Considerations: Embracing Cobots Responsibly
Despite the numerous advantages, the implementation of cobots presents certain challenges that need to be carefully addressed for successful integration into the manufacturing process. One such challenge is the limited payload capacity of cobots compared to traditional industrial robots, which may restrict their use for tasks involving heavy objects or large components. Manufacturers need to carefully evaluate the weight and size of materials being handled to determine if a cobot is the most appropriate solution.4
Another challenge is the programming complexity of cobots. Although they are generally easier to program than industrial robots, they may still require some level of technical expertise for complex tasks. This can be a hurdle for smaller manufacturers who may not have the in-house expertise to program and maintain cobots effectively.4
Furthermore, the upfront cost of acquiring and integrating cobots can be a barrier for smaller manufacturers, particularly those with limited budgets. The initial investment in cobot technology needs to be weighed against the long-term benefits it offers in terms of increased productivity, reduced labor costs, and improved safety.1,3
Latest Advances in Cobot Tech
Recent research has demonstrated the ongoing progress in cobot technology. Researchers are focusing on improving the intelligence and autonomy of cobots through the use of artificial intelligence (AI) and machine learning algorithms.6
Additionally, cloud-based platforms are being developed that can simplify cobot deployment and control, enabling remote monitoring, programming updates, and data analysis, fostering greater flexibility and scalability for manufacturers. By adopting cloud-based cobot control systems, manufacturers can monitor cobot performance in real-time, troubleshoot remotely, and implement programming updates with ease.6,4
Recent advancements in gripper technology and sensor integration are augmenting the capabilities of cobots, empowering them to handle delicate materials and complex tasks with greater precision. Joint initiatives between academia and industry are propelling the advancement in human-robot interaction, opening up avenues for more intuitive and seamless collaboration between humans and cobots.7
Moreover, cobots-as-a-service (CaaS) models are making cobot technology more accessible to small businesses and startups. The CaaS model enables manufacturers to rent cobots instead of purchasing them outright, offering a flexible and cost-effective way to experiment with cobot technology and scale their cobot usage based on their evolving needs.8
Future Prospects and Conclusion
The future of cobots in manufacturing looks promising, with growing adoption across various industries worldwide. As technology continues to evolve, cobots will become more intelligent, agile, and capable of performing a wider range of tasks. The integration of advanced technologies such as 5G connectivity, edge computing, and augmented reality (AR) will further enhance the capabilities of cobots, enabling real-time data analysis and remote monitoring.
With the growing demand for customized and personalized products, the future of manufacturing will likely involve a harmonious blend of human ingenuity and robotic precision, with cobots acting as valuable partners in the production process.
However, it is imperative to acknowledge the importance of responsible implementation. Manufacturers must invest in providing proper training to their workforce to ensure a seamless transition and effective collaboration with cobots. Additionally, it is crucial to address concerns related to potential job displacement and prioritize ethical considerations in the implementation of cobots.
In conclusion, cobots are revolutionizing the manufacturing landscape, bringing in a new era of automation that prioritizes collaboration, efficiency, and innovation. Despite the challenges, advancements in technology and increased industry collaboration are driving the rapid growth and evolution of cobots.
Looking ahead, cobots will play a fundamental role in shaping the manufacturing industry by providing revolutionary solutions that enable businesses to thrive in a highly competitive global market.
References and Further Reading
- Matheson, E., Minto, R., Zampieri, E. G. G., Faccio, M., & Rosati, G. (2019). Human–Robot Collaboration in Manufacturing Applications: A Review. Robotics, 8(4), 100. https://doi.org/10.3390/robotics8040100
- International Federation of Robotics. (2023, September). Collaborative industrial robots https://ifr.org/
- Bisen, A. S., & Payal, H. (2022). Collaborative robots for industrial tasks: A review. Materials Today: Proceedings, 52, 500–504. https://doi.org/10.1016/j.matpr.2021.09.263
- Liu, L., Guo, F., Zou, Z., & Duffy, V. G. (2022). Application, Development and Future Opportunities of Collaborative Robots (Cobots) in Manufacturing: A Literature Review. International Journal of Human–Computer Interaction, 1–18. https://doi.org/10.1080/10447318.2022.2041907
- Prabhakaran, S., Shudhi Rishaa, P., Ashwath, R., & Suresh, M. (2024). A review on cobots: A man’s helping hand. AIP Conf. Proc., 3035(020027). https://doi.org/10.1063/5.0194713
- Riliwan Adekola Adebayo, Nwankwo Constance Obiuto, Oladiran Kayode Olajiga, & Igberaese Clinton Festus-Ikhuoria. (2023). AI-enhanced manufacturing robotics: A review of applications and trends. World Journal of Advanced Research and Reviews, 21(3), 2060–2072. https://doi.org/10.30574/wjarr.2024.21.3.0924
- Alexander Obaigbena, Oluwaseun Augustine Lottu, Ejike David Ugwuanyi, Boma Sonimitiem Jacks, Enoch Oluwademilade Sodiya, Obinna Donald Daraojimba, & Oluwaseun Augustine Lottu. (2024). AI and human-robot interaction: A review of recent advances and challenges. GSC Advanced Research and Reviews, 18(2), 321–330. https://doi.org/10.30574/gscarr.2024.18.2.0070
- Dr. A. Shaji George, A.S.Hovan George. (2023) The Cobot Chronicles: Evaluating the Emergence, Evolution, and Impact of Collaborative Robots in Next-Generation Manufacturing. Partners Universal International Research Journal (PUIRJ) ISSN: 2583-5602, 02(02), 89-116. https://doi.org/10.5281/zenodo.8021406
Disclaimer: The views expressed here are those of the author expressed in their private capacity and do not necessarily represent the views of AZoM.com Limited T/A AZoNetwork the owner and operator of this website. This disclaimer forms part of the Terms and conditions of use of this website.