By Samudrapom DamReviewed by Susha Cheriyedath, M.Sc.Updated on Sep 11 2024
Robotic manipulators have transformed industries by performing tasks with precision and speed far beyond human capabilities. These machines can operate in hazardous environments, mimicking human arm movements to handle complex and specialized tasks.1 From assembly lines to space exploration, robotic manipulators are essential tools in a variety of sectors, including manufacturing, healthcare, and beyond.
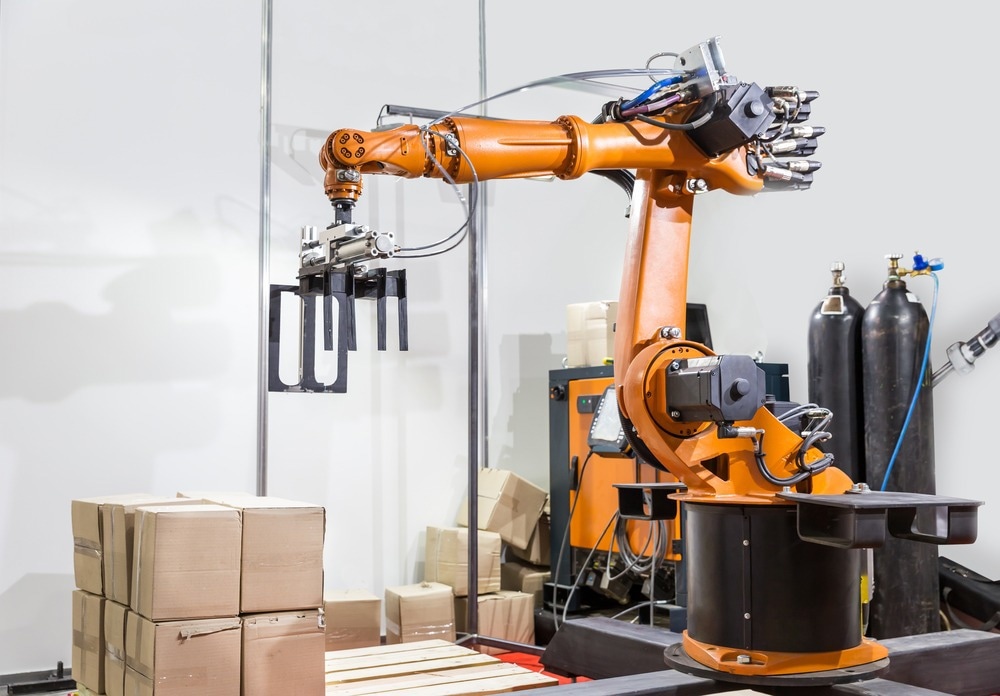
Image Credit: Nomad_Soul/Shutterstock.com
A robotic manipulator is an advanced, electronically controlled system made up of interconnected electric, electronic, and mechanical components. These jointed segments, resembling the movements of a human arm, provide varying degrees of motion and dexterity, allowing the manipulator to carry out precise tasks in diverse environments, from factories to hazardous locations.2
Robotic manipulators are composed of a series of connected segments, or links, that move within a set number of degrees of freedom (DOF)—which can range from two to ten or more. Each DOF corresponds to an axis powered by a motor, giving the manipulator the flexibility to perform a wide range of movements. Most industrial robotic manipulators have four to six axes, with six-axis models being the most common due to their similarity to the human arm, making them versatile enough for automating complex tasks.3
The general structure of a robotic manipulator includes an arm, body, and wrist. The arm and body control the overall movement of the robot within its work envelope, while the wrist maneuvers the end-effector, the part that interacts with the environment to complete tasks like gripping or welding. The design of the manipulator determines its reach, the size of its workspace, and its task efficiency.
Robotic manipulators have been integral to industrial automation for many years. With the ongoing advancements in artificial intelligence (AI), these robots are becoming even more precise and capable, expanding their use across industries. From assembly lines to hazardous material handling, robotic manipulators are continuously evolving, making them indispensable in modern industrial processes.
Kinematics of a Robotic Manipulator
Kinematics govern the movement and task performance of a robotic manipulator.
Kinematics focuses on the motion of the robot’s links and joints without considering the forces that cause the movement. It is essential for understanding how robotic manipulators position their end-effectors (the tool or device attached to the arm, such as a gripper or welder) to complete tasks with precision.
Kinematics are divided into two key types:
- Forward kinematics: This involves calculating the position and orientation of the manipulator’s end-effector based on the known joint angles. For example, forward kinematics is used in manufacturing to predict where the arm will place an object during tasks like assembly or painting.
- Inverse kinematics: This process determines the joint angles required to move the end-effector to a specific location. Inverse kinematics is essential for high-precision tasks, such as robotic surgery or 3D printing, where the end-effector must reach an exact point with accuracy.
In robotic applications like surgical procedures, inverse kinematics ensures the surgical tools are positioned with extreme precision, while in automated manufacturing, forward kinematics helps robots predict the precise placement of components.
Robotic Manipulator Arm Configurations
Robotic manipulators are classified into different types based on the configuration of their joints, each suited to specific tasks:
Cartesian Geometry Arm
This configuration uses prismatic joints to move in straight, linear paths within a rectangular workspace. The simple control mechanism, combined with high mechanical rigidity and precision, makes this configuration ideal for tasks requiring repetitive accuracy, such as robotic X-ray systems, where consistent, precise movements are needed to capture images, and nuclear material handling, where safety and precision are critical.4,5
Cylindrical Geometry Arm
Formed by replacing the waist joint of a Cartesian arm with a revolute joint, this arm moves in cylindrical paths through translation and rotation. It is well-suited for pick-and-place operations, coating applications, and machine loading/unloading.4
Polar/Spherical Geometry Arm
A polar or spherical arm is created by replacing the shoulder joint of the Cartesian arm with a revolute joint, allowing positions to be described using polar coordinates. This configuration offers good weight-lifting capabilities and is typically used in material transfer, stacking and unstacking, machine tool loading, and die-casting.4
Articulated/Revolute Geometry Arm
By replacing the elbow joint of a Cartesian arm with a revolute joint, an articulated arm is formed. This configuration provides a complex, thick-walled spherical workspace, offering greater flexibility in reach. It is commonly used for tasks such as spray painting and welding, where range of motion and reach are crucial.4
Selective Compliance Automatic Robot Arm (SCARA)
This arm has two revolute joints in a horizontal plane, allowing extension in a horizontal workspace. SCARA robots are ideal for pick-and-place operations and are widely used in assembly tasks due to their speed and precision.5
Collaborative Robot Arm
Designed to work closely with humans, collaborative robot arms include safety features to reduce risks in hybrid work environments. These robots are increasingly used in industrial settings where humans and robots work side by side, such as in assembly lines and warehouses.6
Applications
Robotic manipulators are used in a wide range of industries and applications, including:
- Motion planning: Precise control of motion to execute tasks efficiently.
- Remote handling: Performing tasks in hazardous environments, such as handling radioactive materials.
- Teleoperation: Allowing human operators to control robots remotely, often in dangerous or inaccessible environments.
- Micro-robots: Enabling fine, intricate tasks, such as in medical procedures or microassembly.
- Humanoid robots: Mimicking human actions in tasks requiring dexterity and adaptability.
- Machine tools: Enhancing productivity in manufacturing.
- Space operations: Tasks such as maintenance and assembly aboard spacecraft or space stations, including the International Space Station.
- Military EOD (Explosive Ordnance Disposal): Defusing bombs and handling hazardous materials.
- Medical applications: Performing surgeries, including delicate procedures such as keyhole surgery.
Teleoperation is particularly transformative as it allows human operators to control robotic manipulators from a distance. This capability is critical in fields like telemedicine, where robots can perform delicate surgical procedures remotely, reducing human error and improving patient outcomes. In industrial settings, teleoperation enables robots to handle hazardous materials or work in dangerous environments, such as cleaning up after natural disasters or managing nuclear waste.
As AI continues to advance, the potential for autonomous teleoperation is growing. In the future, robots could independently perform tasks based on pre-programmed inputs, further reducing the need for human intervention in high-risk environments.
New Developments
Recent research published in the International Journal of Robotics and Control Systems introduced a new dynamic model for a robotic manipulator with one degree of freedom, incorporating the LuGre friction model. This model enhances control accuracy by accounting for the nonlinear behavior of friction, a common source of error in robot control systems.
Such advancements are crucial for robotic arms used in space exploration, where precise control is required in environments with minimal gravitational forces. Similar improvements are being made for medical robots, allowing for smoother and more accurate movements during surgical procedures.7
Robotics Market in the US: What You Need to Know
In Summary
Robotics has become an essential field across multiple industries, producing machines that can perform tasks faster and more precisely than human counterparts. Robotic manipulators, in particular, have revolutionized sectors such as manufacturing, space exploration, and medicine by improving safety, efficiency, and accuracy.
As AI continues to advance, the future of robotic manipulators holds exciting possibilities. From autonomous decision-making in manufacturing to seamless human-robot collaboration in healthcare, these machines are set to play a larger role in industries across the globe. With the ability to learn and adapt to new tasks, robotic manipulators will expand their applications and become indispensable in an increasingly automated world.
References and Further Reading
- Pires, J.N. (2007). Robot Manipulators and Control Systems. Industrial Robots Programming. DOI: 10.1007/978-0-387-23326-0_2, https://link.springer.com/chapter/10.1007/978-0-387-23326-0_2
- What is a Robotic Manipulator? A Guide [Online] Available at https://www.evsint.com/what-is-a-robotic-manipulator-a-guide/
- Robotics: Structure of Industrial Robots or Manipulators: Types of Base Bodies – I [Online] Available at https://www.brighthubengineering.com/robotics/26371-robotics-structure-of-industrial-robots-or-manipulators-types-of-base-bodies-one/
- Robot Arm Configurations [Online] Available at https://www.eeweb.com/robot-arm-configurations/ (Accessed on 11 September 2024)
- Arteaga, M.A., Gutiérrez-Giles, A., Pliego-Jiménez, J. (2022). A General Overview of Robot Manipulators. Local Stability and Ultimate Boundedness in the Control of Robot Manipulators, 3-14. DOI: 10.1007/978-3-030-85980-0_1, https://link.springer.com/chapter/10.1007/978-3-030-85980-0_1
- Bernier, C. (2022) Robotic Arms: Different Types and When to Use Them [Online] Available at https://howtorobot.com/expert-insight/robotic-arms (Accessed on 11 September 2024)
- Junior, J. A. L., Balthazar, J. M., Ribeiro, M. A., Janzen, F. C., Tusset, A. M. (2023). Dynamic model of a robotic manipulator with one degree of freedom with friction component. International Journal of Robotics and Control Systems, 3(2), 315-329. DOI: 10.31763/ijrcs.v3i2.984, https://pubs2.ascee.org/index.php/IJRCS/article/view/984
Disclaimer: The views expressed here are those of the author expressed in their private capacity and do not necessarily represent the views of AZoM.com Limited T/A AZoNetwork the owner and operator of this website. This disclaimer forms part of the Terms and conditions of use of this website.