These capabilities include intricate operations and tasks, including the manipulation and grasping of objects within their respective operational domains. The most widely employed sensors for estimating contact geometry and force are GelSight sensors. However, researchers have recently introduced an innovative Gellight sensor with significantly improved sensing capabilities, demonstrating its potential as a groundbreaking advancement in this field.
In recent years, using Vision-based Tactile Sensors (VBTS), including GelSight sensors and their variations, has emerged as an effective method for acquiring tactile and force-related data. The fundamental principle of GelSight sensing involves the reconstruction of soft elastomer deformations caused by external objects, utilizing images obtained through an integrated camera. Furthermore, this technique allows for determining both normal and shear forces in addition to contact geometry.
Thanks to their cost-effectiveness, ease of replication, and the ability to achieve pixel-level spatial resolution in measurements, GelSight sensors have significantly expanded the capabilities of robots in various grasping applications. These applications include handling delicate objects, manipulating deformable items, and classifying material.
Challenges Faced by the Robotics Industry in Developing Tactical Sensors
Presently, tactile sensing devices remain in a state of limited maturity, particularly due to the complexities associated with understanding the intricacies of human touch and the challenges of replicating it in hardware. A study published in IEEE Sensors Journal states that several challenges have to be faced during the development of an industrially certified sensor.
Primarily, the sensor's size must be compact to align with standard robot dimensions. It should consistently deliver real-time force and tactile feedback with high signal quality, which usually requires a complex framework. The sensor's reproducibility is also essential, allowing fellow researchers to replicate it.
The capacity to measure both normal force and shear force, along with torque, is a major challenge. Lastly, the sensor should adeptly handle multi-point touch rather than being limited to single-point touch, ensuring an evenly distributed contact area where each local tactile element ideally shares the same characteristics.
Additionally, a study published in IEEE Xplore has also pointed out that tactile sensing applications have encountered certain limitations, with their progress in recent years noticeably lagging behind the remarkable advancements in computer vision. A primary contributing factor to this disparity is that, from a hardware standpoint, existing robotic tactile systems do not match the effectiveness or compactness of their human counterparts.
What Improvements Are Needed by the GelSight Sensor?
The force sensing mechanism employed by GelSight sensors faces two notable limitations. First, it cannot measure forces when the elastomer undergoes uniform deformation, such as when in contact with a large, flat surface. This limitation arises because the reconstruction of the elastomer's surface normal becomes obstructed, as changes in brightness cannot be effectively captured by the camera.
Second, the range of force sensing is constrained by the thickness of the elastomer; it saturates when the elastomer reaches its deformation limit. This saturation issue becomes more pronounced as newer GelSight designs opt for thinner elastomers, thus imposing restrictions on the sensing range.
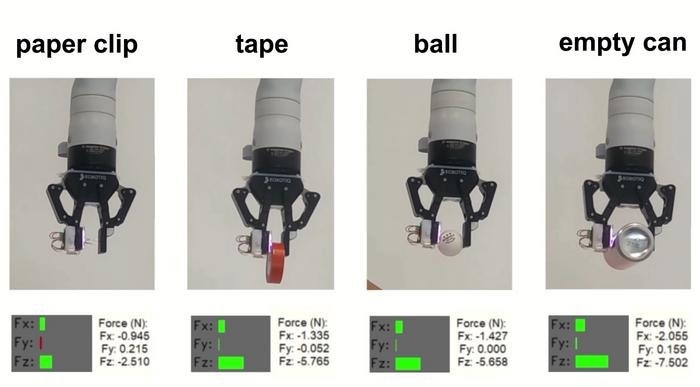
The sensor feeling the objects. Image Credit: F-TOUCH Team
Latest Research Findings
Researchers have proposed an L3 F-TOUCH multi-axis sensor in IEEE Robotics and Automation Letters equipped with a simple suspension framework of springs and elastomer structure with a GelSight sensing mechanism. The elastomer structure serves a dual purpose; it not only reconstructs contact geometry but also undergoes three-dimensional elastic displacement, which can be converted into a three-axis force measurement with a substantially wider range when compared to the capabilities of a GelSight sensor.
L3 F-TOUCH is both lightweight and cost-effective, given that the suspension structure and tracking mechanism do not necessitate the integration of new sensors. Secondly, the concurrent yet independent measurement of tactile feedback and force, derived from a single image, enables users to tailor a wireless camera module for real-time image streaming.
The linearity assessment of L3 F-TOUCH sensors yielded root mean square error (RMSE) values of 0.2346 N, 0.1573 N, and 1.33 N, accompanied by R-square values of 0.96, 0.96, and 0.87. Notably, the sensor demonstrated robust linearity within the defined range of ±2 N in the xy plane and 12 N in the z direction.
The robot was assigned the task of grasping a potato chip delicately, without causing any damage. Interestingly, both the elastomer, which quantifies force through Gel deformation and the suspension structure, which gauges force via elastic displacement, yielded comparable force measurements in the normal direction (Fz). This observation suggests that the newly proposed suspension structure is equally proficient in capturing minor forces as conventional GelSight sensors.
Future Direction
In the domain of robotics, future research works will emphasize the expansion of sensor capabilities from measuring three-axis force to encompassing six-axis force and torque measurements, all while maintaining precision and compactness.
Elevating sensor sensitivity can be attained through refinements to the suspension structure, while the enhancement of wireless transmission can be achieved by optimizing protocols and decoding configurations. These advancements hold the promise of endowing robots with a heightened sense of touch, enabling them to engage in more dynamic and agile manipulation tasks, including scenarios such as aerial manipulation.
References and Further Reading
Li, W., et al. (2023) L3 F-TOUCH: A Wireless GelSight With Decoupled Tactile and Three-Axis Force Sensing. IEEE Robotics and Automation Letters, 8(8), pp. 5148-5155, doi.org/10.1109/LRA.2023.3292575.
Li, W., et al. (2021) F-TOUCH Sensor: Concurrent Geometry Perception and Multi-Axis Force Measurement. IEEE Sensors Journal, 21(4). pp. 4300-4309. doi.org/10.1109/JSEN.2020.3030631
Althoefer, K., et. al. (2023). A Miniaturised Camera-based Multi-Modal Tactile Sensor. arXiv preprint arXiv:2303.03093. Available at:
doi.org/10.48550/arXiv.2303.03093
EurekAlert, 2023. Researchers develop low-cost sensor to enhance robots' sense of touch. [Online] Available at: https://www.eurekalert.org/news-releases/996956
Disclaimer: The views expressed here are those of the author expressed in their private capacity and do not necessarily represent the views of AZoM.com Limited T/A AZoNetwork the owner and operator of this website. This disclaimer forms part of the Terms and conditions of use of this website.