Jun 27 2012
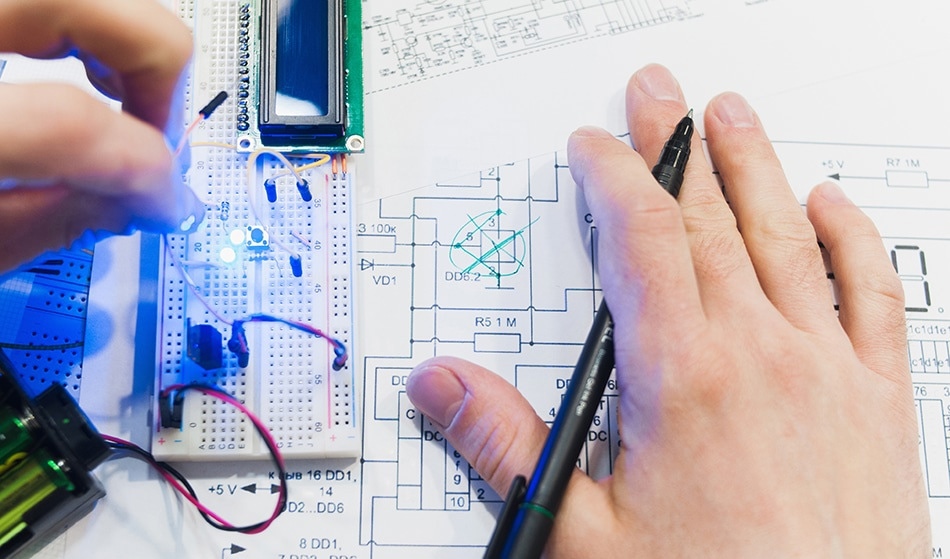
Image Credits: Golubovy/shutterstock.com
Mechatronics is a study that fuses mechanical engineering and electronic engineering. Current working definitions of mechatronics describe this study as a multidisciplinary field of engineering that includes a combination of computer engineering, software engineering, control engineering, and systems design engineering for the design and manufacture of products. By using computer design software, there is the added flexibility to the re-engineering of programming and data collection methods.
Sophisticated mechatronic systems are applied in the design of cars, robotics, and industrial machines. During the design process of a product, there has to be an organized and well-thought-out integration of mechanical, electronic, and control engineering to ensure that the end product is as flexible and reliable as is possible when competing with similar products on the market. A working principle of mechatronics also needs a fusion of sensor, measurement, actuation, and microprocessor technology combined with an analysis of how systems behave when integrating. Industrial production systems are built with mechatronic systems that work together to control a piece of machinery. There is an architectural system to mechatronic systems controlled by algorithms:
- Hierarchy – The arrangement of objects, names, and values in the order of superiority or functional ability.
- Polyarchy – The dispersion of function responsibility across a set of systems.
- Heterarchy – A working system with mixed function.
- Hybrid – A product or functional system as a by-product of merging two separate functional entities. Such hybrid systems include production systems, automotive sub-systems, and cameras.
The Design Process
Mechatronic systems are designed in a number of stages that are summarized as follows:
Stage 1
Defining a need (i.e., analysis of market research reports and client feedback).
Stage 2
Analyzing the need. User requirements allow for a clear understanding of the systems specifications for the design of a machine, which is crucial for user satisfaction. This stage is most challenging to the design process as it involves integrating all customer requirements to design a system that compliments all user needs. The identification process needs to design an accurate representation of the end system.
Stage 3
Conceptual design. After establishing system requirements, needs have to be implemented into a model. While implementing a model, a cost-benefit analysis is fundamental. It is important to generate solutions and concepts through the application of 3D graphical virtual displays to demonstrate a particular design to the end user.
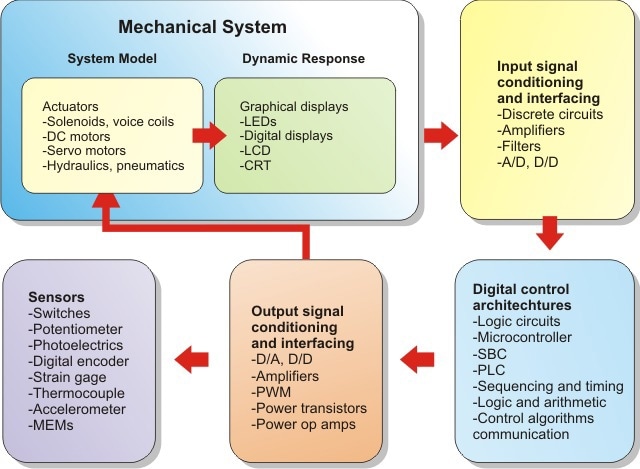
Stage 4
The integration of mechanical, electronics, sensor, and software technology into the design. This stage involves the design of all mechanical parts and a system design. During this process, computer-aided design and computer-aided electronic tools are commonly applied to illustrate individual components of a mechanical system. Kinematics properties, sensor, and actuator function also need to be established during such an integration process to achieve the optimal mechanical design.
Stage 5
Production and simulation of a detailed mechanical design. During the production phase of a mechanical design model, electrical components are integrated to test the model function. At this stage, the model should encompass the physical system with input/output control and flexibility and measuring parameters. Certain specifications are paramount to understanding the functional capacity to a working mechatronic system, including steady-state error, bandwidth, phase margin, time constants, and peak time. By putting the mechatronic system through simulation, all selected design specifications should perform as expected. Any error in the design specifications should be modified into a new control structure that does satisfy the initial design specifications.
Stage 6
Following the simulation of a mechatronic system and provided that all design specifications are met, the design system is then transformed into a prototype during which the design collaborates with industrial users.
Measurement Systems
There three basic measurement systems to mechatronic technology:
- A sensor is used to generate an output signal to the quantity of a particular parameter being measured.
- There is a signal conditioner that will interpret the signal output and present this signal in a form that can be observed by the end user.
- A display system may be used either as a scale or a display console.
A popular example of a basic mechatronic system is that of a thermometer. The video below demonstrates the simulation of mechatronic systems with multi-body dynamic control systems.
Simulation of Mechatronic Systems
New Research Areas
Mechatronics have already been proven useful in automotive systems, biological engineering, biomedical applications, real-time imaging, topology organization, and energy systems. Considering these current mechatronic applications, research in mechatronic systems is now focusing on learning capabilities and self-adaptation to make these systems more sophisticated and user-friendly.
For instance, there is an emphasis on looking at how neural networks function and how this can be used in software applications to implement better command options. Such efforts will be fundamental to perfecting a mechatronic system that would allow machines to integrate with humans more effectively.
Sources and Further Reading
This article was updated on 7th February, 2019.